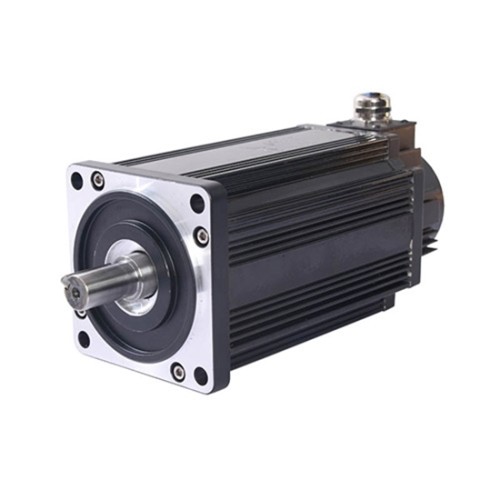
- Stock: In Stock
- Model: SCJ009208
- SKU: SCJ009208
Available Options
Ask a Question About This Product
- Description
500W 48V Brushless DC Servo Motor, 3 Nm, 1500 rpm
Brief
Description
High performance 48V DC servo motor with incremental encoder, brushless design, 500W power rating, 1500 rpm rated speed, 3 Nm holding torque, come with international standards, through CE, ISO certification.
Basic Specifications
- Model: ATO-110AS0405-15
- Rated Power: 500W
- Rated Voltage: 48V DC
- Rated Current: 14 A
- Rated Torque: 3 Nm
- Peak Torque: 10.8 Nm
- Rated Speed: 1500 rpm
- No-load Speed: 1700 rpm
- Working Efficiency: 85%
- Flange Size: 110mm
- Weight: 7 kg
Technical Parameters
- Incremental Encoder Line: 2500 PPR
- Rotary Inertia: 560 Kg.m2x10-6
- Line Resistance: 0.13 Ω
- Armature Inductance: 180 μH
- Torque Constant: 0.22 Nm/A
- Brake Apparatus Voltage: 24V DC, brake release when powered
- Motor Lead Length: 1 meter
- Back EMF: 17.3 vkr/min
- Protection Grade: IP55
- Insulation Class: Class F
- Certification: CE, ISO
Features
- 500W DC servo motor with IP55 protection grade and F class insulation structure
- Optimized winding end structure, minimized copper loss and iron loss, small size, light weight, low temperature rise and high efficiency (85%)
- Super coercivity, SOCOJE DC brushless servo motors using NdFe35 permanent magnet material, strong anti-demagnetization ability, stable motor performance
- Low noise, low vibration, low moment of inertia
- High torque, fast dynamic response, wide speed range, strong overload capacity (4 times)
Dimension (Unit=mm)
Wiring Definition
Details
Tips: PWM control the DC motor
The PWM speed-regulation principle of DC motor is different from that of AC motor. By adjusting the pulse width of the driving voltage and working with some corresponding energy storage elements rather than adjusting the speed of the motor by frequency modulation, it changes the amplitude of the voltage transmitted to the armature, so as to change the speed of the DC motor. Therefore, its modulation mode is to modulate the amplitude.
In brushless DC motor controlled by PWM, there are two ways of PWM control:
- When PWM signal is used to control the conducting time of the transistor, the longer the conducting time is, the longer the working time is, and higher the speed of the motor is.
- PWM signal is used to control the conducting time of transistor and change the control voltage.
PWM refers to regulating pulse width, namely, regulating the time ratio of high level to low level of square wave. A 20% duty cycle wave will have 20% of high-level time and 80% of low-level time , while a 60% duty cycle wave will have 60% of high-level time and 40% of low-level time. The larger the duty cycle and the longer the high-level time are, the higher amplitude the output pulse is, that is, the higher the voltage is.
- Reviews