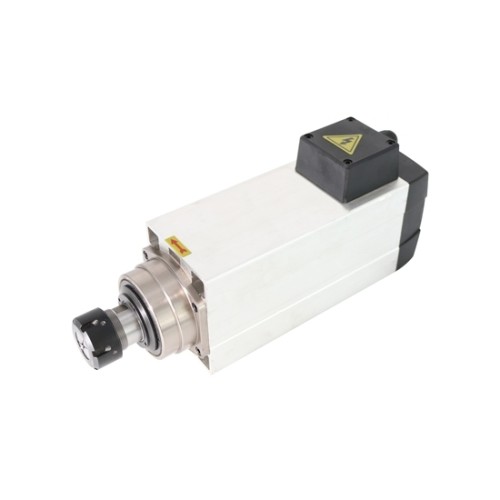
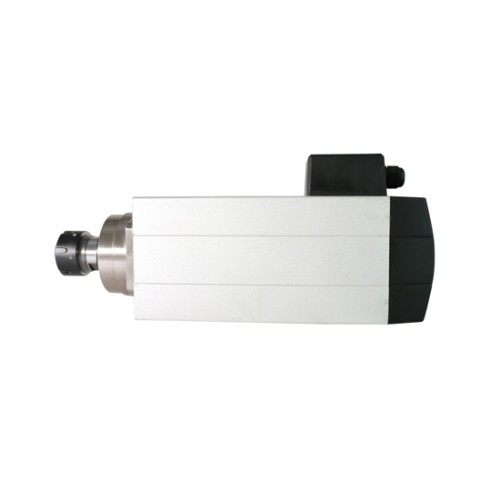
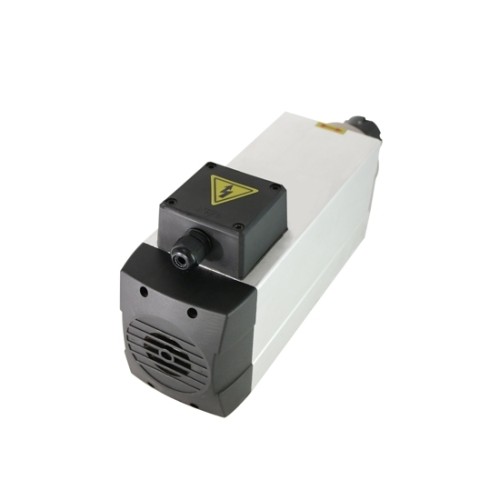
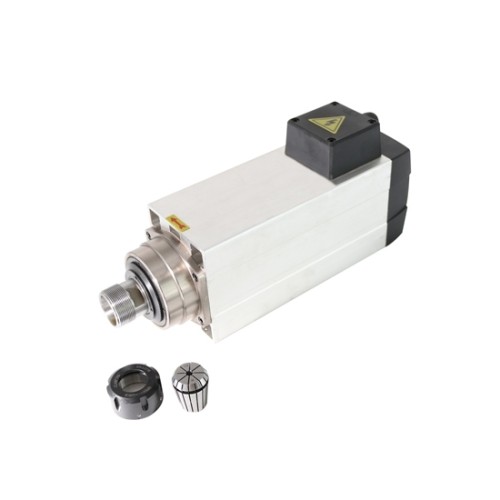
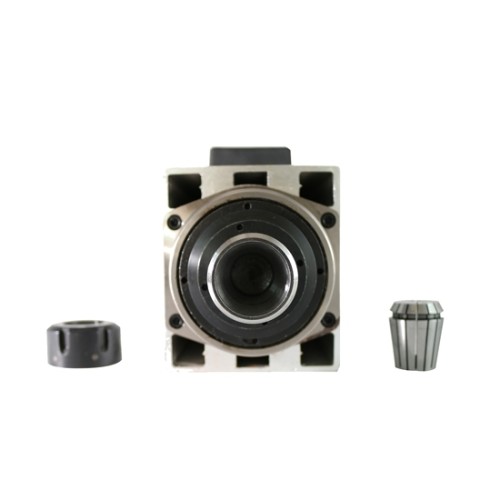





- Stock: In Stock
- Model: SCJ009532
- SKU: SCJ009532
Available Options
Ask a Question About This Product
- Description
6 kW Air Cooled CNC Spindle Motor 18000 rpm ER32
Brief
Description
6 kW CNC spindle motor, 18000 rpm speed, 2.78 Nm torque, 300Hz frequency, 3 phase 380V AC operating voltage, ER32 (φ3.175 mm - φ20 mm) collet.
Feature
- Spindle motor with air cooling fan and ER32 collet ensures smooth running.
- Fast response, strong overload capacity, low noise and high mechanical precision.
- High quality 4 pcs bearings (7008Cx2 + 7002Cx2), runout off less than 0.01mm, tapered bore less than 0.005mm.
- P4 grade ceramic ball bearings used as spindle bearing, which improves the service life under high speed revolution.
- Lubricated with grease, which is resistant to 200 degrees high temperature.
- Tight sealing and two-layer dustproof design.
Application
This series air-cooled electric spindle motors mainly match with variable frequency drives or engraving machines, CNC router machine, and used for high speed profiling, drilling, cutting, engraving and groove milling of wood, metal, plastics, foam, rubber and other materials.
Note: The spindle motor and VFD shall be suitable with each other. The specifications and parameter settings of the VFD shall match the nominal parameters of the spindle motor. Otherwise, it will burn the spindle motor if the settings are not correct.
Specification
Model | STF60-103-6.0 |
Matched VFD Model | GK3000-4T00110G (15 hp three phase VFD) GK3000-CS00110G (15 hp 1-phase 220V to 3-phase 380V VFD) |
Power | 6 kW |
Phase | Three phase |
Speed | 18000 rpm |
Voltage | 3-phase 380V±10% AC |
Current | 12.8A |
Frequency | 300Hz |
Torque | 2.78 Nm |
Number of Pole | 2 poles |
Cooling Type | Air-cooled |
Installation Method | Horizontally or Vertically (When the motor is installed, the radial runout standard is required to be within 5um, and the chuck is generally 10um-15um.) |
Lubrication | Grease |
Thermal Class | Class F |
Protection Class | IP50 |
Certification | CE |
Warranty | Bearings for half a year, other parts for one year |
Joint of Nose | ER32 (φ3.175 mm - φ20 mm) |
Bearings Type | 7008C P4*2 & 7002C P4*2 |
Application | Woodworking & Plastic |
Weight | 14 kg |
![]() | 6kW Air Cooled Spindle Motor CAD Drawings |
Details
Tips: Motor Speed is a Key Factor When Selecting a CNC Spindle
For high-speed spindle motors, whether light metal processing or heavy metal processing, the motor speed is selected according to the nature of the processed material. The reason why the material with high processing density should be 24000~60000 rpm is because the material has high density, strong hardness, and low-speed processing will cause travel burrs and uneven surfaces. The reason why 3000-24000 rpm is selected for processing low-density materials is that high-speed rotation has the risk of cracking for low-density materials. So when choosing a high-speed CNC spindle motor, the first choice is its speed.
Safety Use
Safety Tips for Using SOCOJE CNC Spindle Motors
1. The electric spindle motor and VFD shall be suitable with each other. The specifications and parameter settings of the VFD shall match the nominal parameters of the spindle motor, and it will burn the spindle motor if the settings are not correct.
2. Before using water-cooled spindle motor, it shall ensure that cooling cycle system works normally and the running under no cooling conditions is prohibited. The volume of cooling water is calculated as per 1 liter/minute, the minimum flow of cooling water is not less than 5 liter/minute, cooling water pipe and the nozzle shall be connected reliably and there is no leakage.
3. The cooling liquid shall be clean and free of grease and the temperature shall be within 5-30℃. The cooling medium shall carry out force cooling when the ambient temperature is higher than 30℃. The precision lathe requires the cooling liquid with a constant temperature of 20 +/-2℃.
4. During storage and transport of the spindle motor, the status of high-speed grease inside the bearing will change. The user shall run it at a low speed first by starting from the lowest speed of the spindle motor for 30 minutes and then 20 minutes for every 3000 rounds. Otherwise there will have abnormal sound, noise, heat and other phenomena, which will affect the bearing life if the spindle motor is started directly at a high speed. During long term storage, the spindle motor shall run (at low speed) for 15-30 minutes once a week at last.
5. Collet, nut and inner taper hole shall be washed clean when installing blades on the spindle motor in order to avoid any impact on the precision. The blade handle shall be inserted into the collet more than 15mm.
6. For daily machining, the spindle motor shall be warmed up, run for 15-20 minutes when the machining speed is reached and then performs precise machining. It is better to stop the spindle motor for two hours every day in order to recover its mechanical fatigue and prolong its life time.
7. No knocking the end cover of the spindle motor. No hammering the collet and blade head when removing blades. No shocking or colliding during transport, storage and using, especially the end of the spindle motor.
8. The spindle motor shall run in designated direction.
9. The spindle motor shall be installed and fixed according to the relevant drawings and instructions.
10. The temperature shall be within 22-25℃ if water cooling machine is used.
11. The spindle motor adopts vapor lock and the gas source shall not be used until it has passed oil-water separator and dry filter. The air pressure is 0.2-0.25Mpa and the filtering precision is 5μm, otherwise there will cause damages to the bearing.
Documents
- Reviews