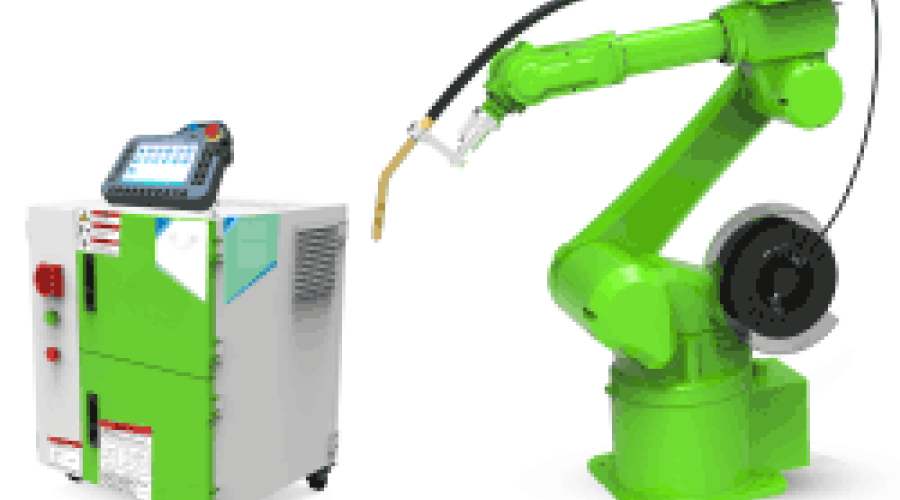
Automatic welding machines have transformed the welding industry by revolutionizing the way welding processes are carried out. These machines, equipped with advanced technology and sophisticated features, provide significant advantages in terms of efficiency, precision, and safety. This article explores the technical aspects and recent advancements in automatic welding machines, highlighting their impact on various industries.
Robotic welding systems are at the forefront of automatic welding machines. These systems utilize industrial robots with articulated arms and advanced sensors to perform welding operations with exceptional precision. The robots can be programmed to follow specific welding paths, ensuring consistent weld quality and minimizing human errors. Additionally, robotic welding systems offer high-speed welding capabilities, resulting in increased productivity and reduced production time.
Automatic welding machines incorporate advanced process control technologies to achieve optimal weld quality. Closed-loop feedback systems, such as real-time monitoring and adaptive control, constantly analyze welding parameters, such as voltage, current, and wire feed speed, to ensure the desired weld characteristics are maintained. This level of control enhances weld penetration, reduces defects, and improves overall weld quality.
Vision systems and sensors play a crucial role in automatic welding machines by providing real-time feedback and precise guidance. Vision systems use cameras to capture images of the welding area, enabling the machine to detect variations in joint alignment and adjust the welding trajectory accordingly. Additionally, sensors monitor variables such as arc length, wire position, and weld pool size, ensuring optimal weld formation and consistency.
The integration of artificial intelligence (AI) technologies is a significant advancement in automatic welding machines. AI algorithms can analyze large datasets of welding parameters, weld defects, and performance indicators to identify patterns and optimize welding processes. This integration enables predictive maintenance, early fault detection, and adaptive control, leading to improved efficiency, reduced downtime, and enhanced overall equipment effectiveness (OEE).
Automatic welding machines now offer remote monitoring and connectivity features, allowing operators to monitor and control the welding process from a central location. This capability enables real-time troubleshooting, remote parameter adjustments, and performance analysis. Additionally, connectivity enables seamless integration with manufacturing execution systems (MES) and other production management tools, facilitating data exchange and enhancing overall manufacturing efficiency.
Automatic welding machines continue to evolve, offering significant advancements in efficiency and precision. Through the integration of robotic systems, advanced process control, vision systems, AI, and remote monitoring capabilities, these machines have transformed the welding industry. The enhanced productivity, improved weld quality, and reduced downtime provided by automatic welding machines have made them indispensable tools in various industries, including automotive, aerospace, construction, and manufacturing. As technology continues to advance, we can expect further innovations in automatic welding machines, further enhancing their performance and expanding their applications in the welding industry.
Leave a comment