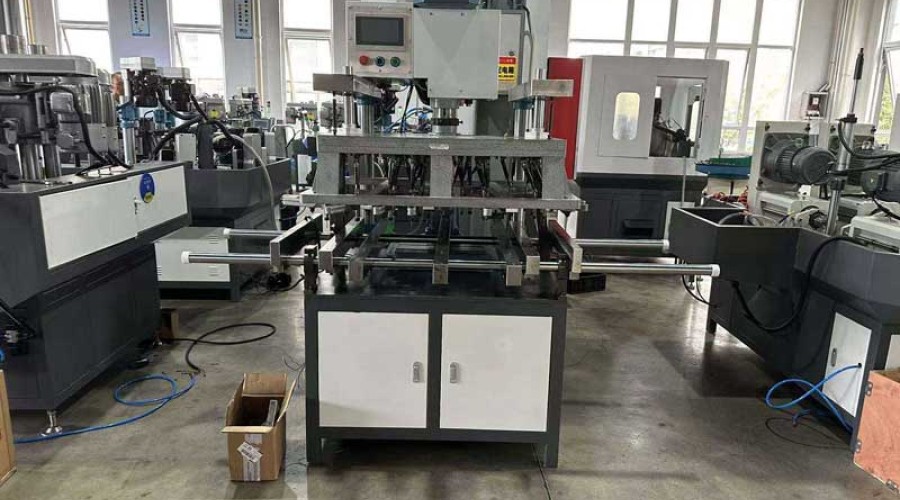
Currently, the development of CNC machine tools is advancing by leaps and bounds. High-speed, high-precision, compound, intelligent, open, parallel drive, networked, extreme, and green have become the trends and directions of CNC machine tool development.
As a manufacturing powerhouse, China still relies mainly on comparative advantages in labor, price, and resources. However, there is still a significant gap in technological innovation and independent development compared to foreign counterparts. The CNC industry in China cannot be content with the status quo. It should seize opportunities for continuous development, strive to develop its advanced technology, increase efforts in technological innovation and talent training, enhance comprehensive service capabilities of enterprises, and work towards narrowing the gap with developed countries. China aims to achieve the transformation of CNC machine tool products from low-end to high-end, from processing basic products to manufacturing high-precision products, realizing the transition from "Made in China" to "Created in China" and from a manufacturing giant to a manufacturing powerhouse.
1.High-speed:
With the rapid development of industries such as automotive, defense, aerospace, and the application of new materials such as aluminum alloys, the demand for high-speed machining of CNC machine tools is increasing.
- Spindle Speed: CNC machines adopt electric spindles (internally mounted spindle motors), with spindle speeds reaching up to 200,000 r/min;
- Feed Rate: With a resolution of 0.01μm, the maximum feed rate reaches 240m/min, enabling precise processing of complex surfaces;
- Computing Speed: The rapid development of microprocessors provides assurance for the development of CNC systems towards high-speed and high-precision. CPUs have developed into 32-bit and 64-bit CNC systems, with frequencies reaching several hundred megahertz to over a thousand megahertz. Due to the significant increase in computing speed, feed speeds of up to 24-240m/min can still be achieved when the resolution is 0.1μm or 0.01μm;
- Tool Change Speed: Currently, the tool exchange time in advanced foreign processing centers is generally around 1 second, with some as high as 0.5 seconds. German company Chiron has designed the tool magazine in a basket style, with the spindle as the axis and the tools arranged around the circumference, achieving a tool-to-tool change time of only 0.9 seconds.
2.High Precision:
The requirement for precision of CNC machine tools is no longer limited to static geometric precision. The accuracy of machine tool motion, thermal deformation, and monitoring and compensation for vibration are increasingly emphasized.
- Improved CNC System Control Accuracy: Using high-speed interpolation technology to achieve continuous feed with tiny program segments, refining the CNC control unit, and using high-resolution position detection devices to improve position detection accuracy (Japan has developed AC servo motors with internally mounted position detectors with 106 pulses/rev, achieving a position detection accuracy of 0.01μm/pulse). Position servo systems use feedforward control and nonlinear control methods;
- Error Compensation Technology: Utilizing techniques such as backlash compensation, lead screw pitch error compensation, and tool error compensation to comprehensively compensate for equipment thermal deformation errors and spatial errors. Research results show that the application of comprehensive error compensation technology can reduce machining errors by 60% to 80%;
- Adopting grid checking and improving the motion trajectory accuracy of machining centers, and predicting machine tool machining accuracy through simulation to ensure the long-term stability of machine tool positioning accuracy and repeatability, enabling it to perform various machining tasks under different operating conditions and ensure the machining quality of parts.
3.Functional Compounding:
The meaning of compound machine tools refers to achieving or completing various element processing from raw materials to finished products on a single machine tool. According to its structural characteristics, it can be divided into process compound types and process compound types. Process compound machine tools include machining centers such as boring, milling, and drilling compounds, milling-turning compounds, and milling-boring-drilling-turning compounds; process compound machine tools include multi-face multi-axis linked processing compound machine tools and dual-spindle turning centers. Using compound machine tools for processing reduces auxiliary time for workpiece loading and unloading, tool replacement, and adjustment, as well as errors generated during intermediate processes, improves part machining accuracy, shortens product manufacturing cycles, enhances production efficiency, and improves manufacturers' market responsiveness, which has significant advantages over traditional dispersed production methods.
4.Control Intelligence:
With the development of artificial intelligence technology and to meet the development needs of flexible manufacturing and manufacturing automation in the manufacturing industry, the degree of intelligence of CNC machine tools is constantly improving. This is specifically reflected in the following aspects:
- Adaptive Control Technology in Machining Process: By monitoring information such as cutting force, power of the spindle and feed motors, current, and voltage during the machining process, and using traditional or modern algorithms for identification, the state of tool force, wear, damage, and the stability of machine tool machining can be recognized. Based on these states, machining parameters (spindle speed, feed rate) and machining instructions can be adjusted in real time to keep the equipment in the optimal operating state, thereby improving machining accuracy, reducing surface roughness, and enhancing the safety of equipment operation;
- Intelligent Optimization and Selection of Machining Parameters: Constructing an "Intelligent Optimization and Selection System for Machining Parameters" based on the experience of process experts or technicians, the general and special rules of part machining, and using modern intelligent methods to obtain optimized machining parameters, thereby improving programming efficiency and machining process level, and shortening production preparation time;
- Intelligent Fault Self-diagnosis and Self-repair Technology: Using modern intelligent methods to achieve fast and accurate fault localization based on existing fault information;
- Intelligent Fault Playback and Fault Simulation Technology: Able to fully record various information of the system, replay and simulate various errors and accidents that occur in CNC machine tools to determine the causes of errors, find solutions, and accumulate production experience;
- Intelligent AC Servo Drive Devices: Intelligent servo systems that automatically identify loads and adjust parameters, including intelligent spindle AC drive devices and intelligent feed servo devices. These drive devices can automatically identify the rotational inertia of motors and loads and automatically optimize and adjust control system parameters, enabling the drive system to operate at its best;
- Intelligent 4M CNC System: In the manufacturing process, integrated machining and inspection are effective ways to achieve rapid manufacturing, rapid inspection, and rapid response. By integrating Measurement, Modelling, Manufacturing, and Manipulator (4M) in one system, information sharing is realized, promoting the integration of measurement, modeling, machining, clamping, and operation.
Domestic CNC machine tools lack core technology, with basic components of high-performance CNC systems and key functions mostly relying on imports. Even though some domestic manufacturers have managed to establish their own brands in recent years, the functionality, performance, and reliability of their products still have a certain gap compared to foreign products. In recent years, domestic CNC machine tool manufacturers have acquired some advanced CNC technologies through technology introduction, domestic and foreign mergers and acquisitions, and foreign procurement. However, there is a lack of research on basic technologies such as machine tool structure and precision, reliability, and humanized design, neglecting the cultivation of independent development capabilities. The technological level, performance, and quality of domestic CNC machine tools still
Leave a comment