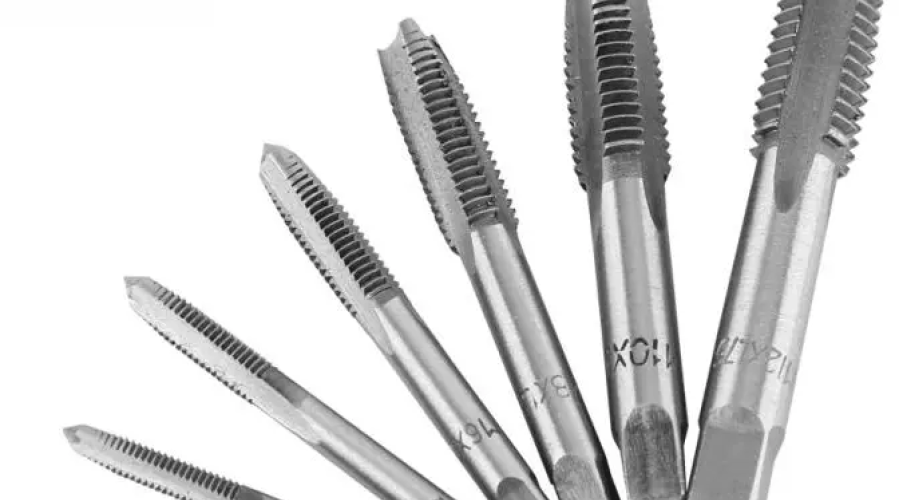
In the complex and ever-changing scenes of metal processing, do you know how to choose the right tap? Today, let's introduce the characteristics of different types of taps.
According to the chip flute type, cutting taps can be divided into straight flute type, spiral flute type, and pointed spiral flute type. The different blade edges and cutting surface forms determine the direction of chip removal.
Straight flute taps discharge chips in any direction through their side surfaces, often used for processing short-chip materials such as cast iron.
Spiral taps are the most common type, they discharge chips upwards and are mainly used for threading blind holes.
However, due to the need for chip removal, the chip flutes of spiral taps are usually ground deeper, resulting in a relatively fragile central portion that is prone to breakage.
Pointed taps, also known as bottoming taps, are the opposite of spiral taps, they discharge chips downwards and are suitable for processing through-hole threads.
If pointed taps are used to process blind holes, the chips cannot be discharged, which may also lead to tap breakage.
In addition to the above three types of cutting taps, there are also non-chip removal extrusion taps, which use the plastic deformation of the workpiece to process threads and are only suitable for materials with good ductility, such as aluminum alloys, low carbon steel, etc.
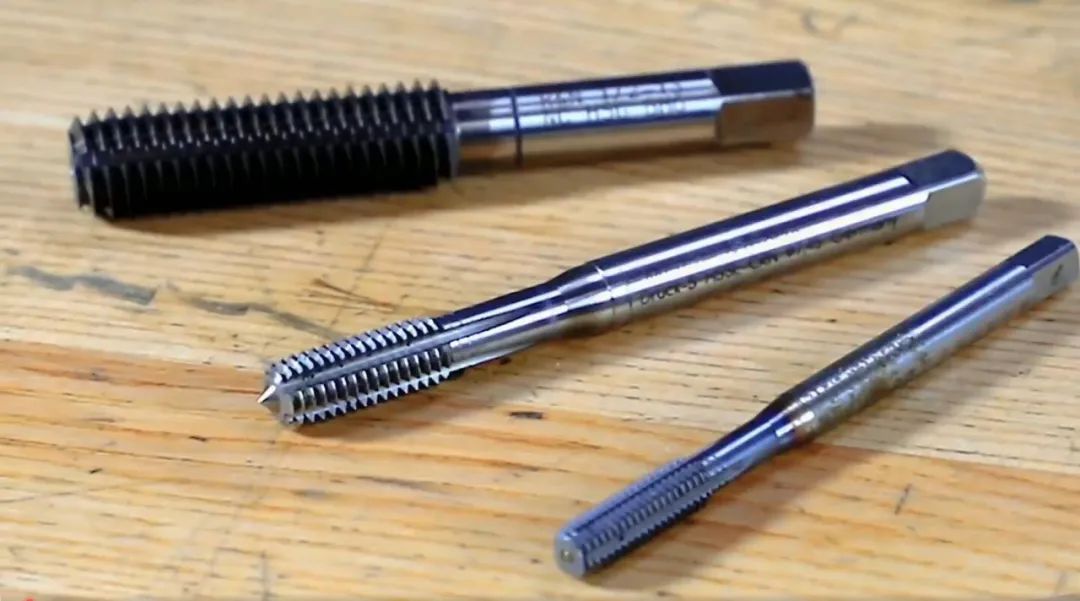
Leave a comment