01 Apr
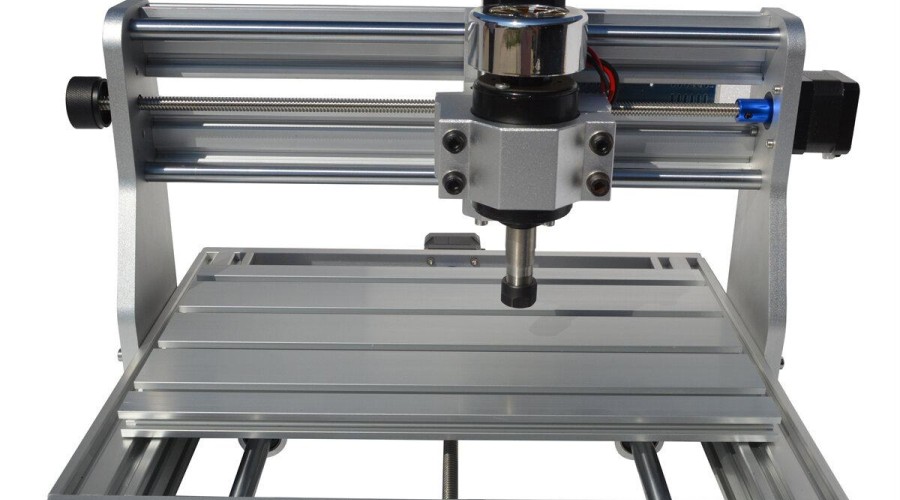
Posted by
0 Comment(s)
318 View(s)
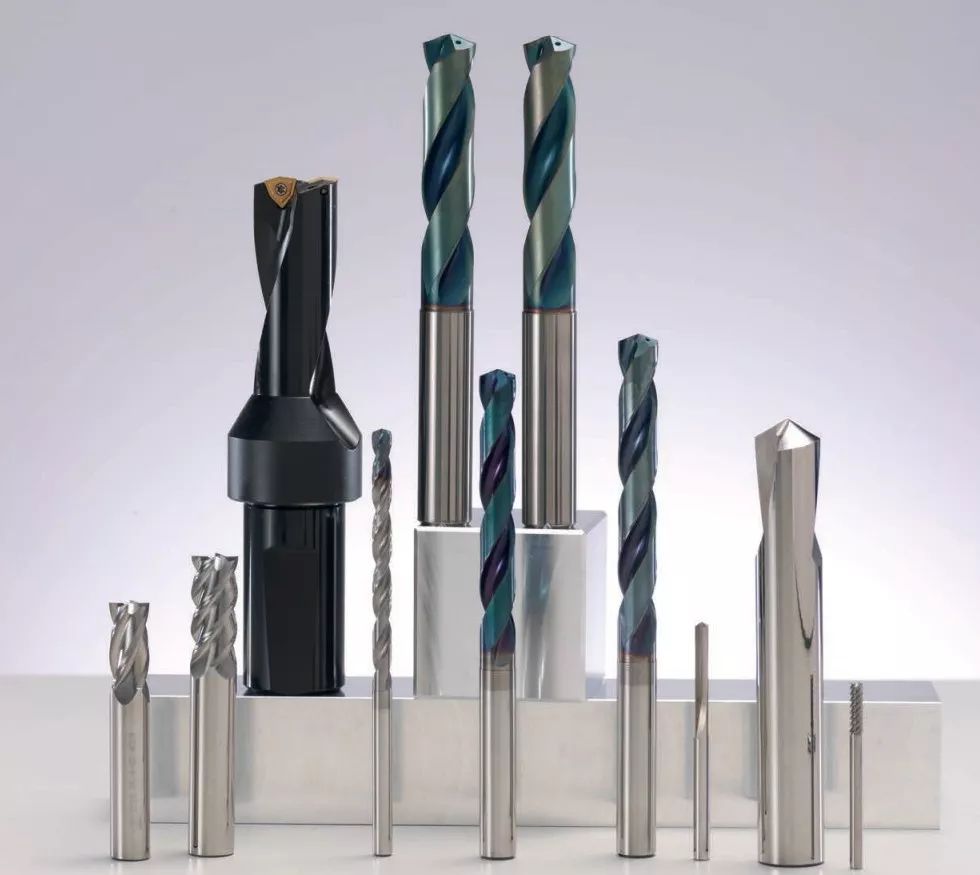
- The drill bit should be placed in a special packaging box to avoid vibration and collision with each other.
- When in use, the drill bit should be taken out from the packaging box and immediately installed into the spring chuck of the spindle or the tool library for automatic tool change. After use, it should be promptly returned to the packaging box.
- Measurement of the drill bit diameter should be carried out using non-contact measuring instruments such as a tool microscope to avoid damage to the cutting edge caused by contact with mechanical measuring instruments.
- Some CNC drilling machines use positioning rings while others do not. If using positioning rings, the depth positioning during installation must be accurate. If not using positioning rings, the protruding length of the drill bit installed on the spindle should be adjusted uniformly, especially for multi-spindle drilling machines, to ensure consistent hole depth. Inconsistent depth may lead to drilling through the workpiece or inability to drill through the circuit board, resulting in scrap.
- Regularly inspect the concentricity of the spindle and the spring chuck, as well as the clamping force of the spring chuck. Poor concentricity may cause problems such as drill bit breakage for small diameter drills and oversize hole diameter. Insufficient clamping force may result in actual speed not matching the set speed and slippage between the chuck and the drill bit.
- The clamping length of the drill bit on the spring chuck should be 4-5 times the diameter of the drill shank to ensure secure clamping.
- Regularly inspect the spindle pressure foot. The contact surface of the pressure foot should be horizontal and perpendicular to the spindle without shaking to prevent drill breakage and off-center holes during drilling.
- The dust collection effect of the drilling machine should be good. Dust collection can reduce the temperature of the drill bit and take away dust to reduce friction and heat generation.
- The substrate and laminates, including upper and lower pads, should be securely positioned and leveled in the hole-slot positioning system on the worktable of the drilling machine. When using adhesive tape, care should be taken to prevent the drill bit from drilling into the tape, causing the drill bit to adhere to the chips and making chip removal difficult, leading to drill breakage.
- When ordering drill bits from manufacturers, 4% of the drill bits should be randomly selected for inspection to see if they meet the specifications. Additionally, 100% of the drill bits should be inspected with a microscope at 10-15 times magnification for notches, scratches, and cracks.
- Drill bits should be re-sharpened in a timely manner to increase their usage and re-sharpening cycles, prolong their service life, and reduce production costs and expenses. Generally, the wear depth within the entire length of the two main cutting edges should be less than 0.2mm. When re-sharpening, 0.25mm should be ground off. Ordinary fixed-handle drill bits can be re-sharpened 3 times, and undercut drill bits can be re-sharpened 2 times. Excessive re-sharpening will decrease the quality and accuracy of the drilled holes and may result in scrap of the finished circuit boards.
- When the wear diameter of the drill bit decreases by 2% compared to the original due to wear, the drill bit should be scrapped.
- The setting of drill bit parameters: In general, manufacturers provide a parameter table for the drilling speed and feed rate of the drill bits produced by the factory. These parameters are for reference only. Actual parameters need to be determined by process personnel based on actual usage. Usually, the actual parameters may differ from the reference parameters, but the difference should not be too significant.
Leave a comment