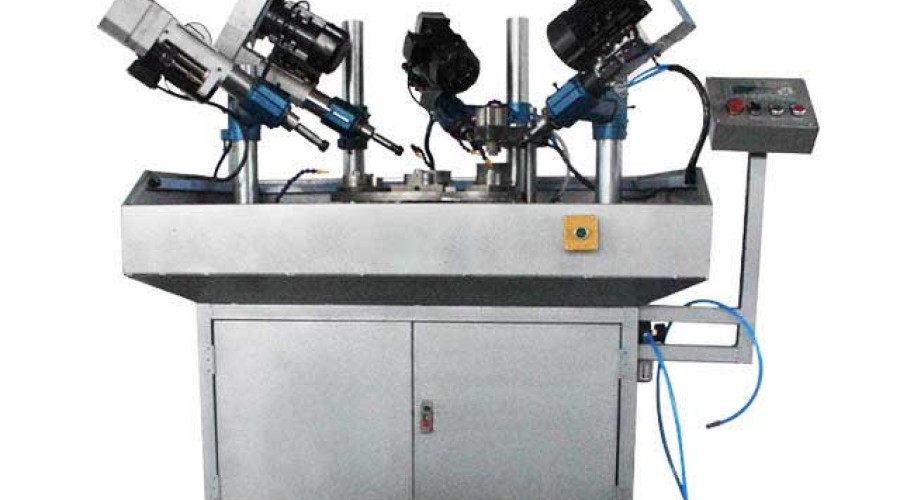
1. Tapping Description
Tapping is the process of creating internal threads, known as tapping, using a tool called a tap. There are several methods for internal thread machining, including the use of taps, thread milling, and cold extrusion. These methods are widely used in different scenarios within the field of machining. However, all these methods require lubrication when threading, traditionally using oil immersion. This lubrication method has several limitations and drawbacks:
- Immersion lubrication can waste a significant amount of lubricant.
- Chips easily adhere to the surface of the workpiece, making cleaning difficult.
- Deep tapping can cause poor chip evacuation, which may damage the tap and thread milling cutter. How can high-precision thread cutting be achieved?
2. Factors Affecting Thread Precision
Management of the Pilot Hole: The tap is a tool that cuts close to the pilot hole. If the pilot hole is not precise, the thread's accuracy will suffer, and the tap's lifespan will be significantly impacted.
Limitations of Tap Machining: When machining threaded holes with taps, the limited chip evacuation space can easily cause chip blockage, leading to the formation of low-precision threads or even tap breakage.
Proper Lubrication Method: Traditional oil immersion lubrication can lead to chip blockage.
3. Methods for Machining High-Precision Threaded Holes
Proper Pilot Hole Machining: The pilot hole must be machined to the appropriate size, considering the thread's engagement rate. It's recommended to use ultra-short carbide drills with high runout accuracy and rigidity. Additionally, using an end mill for contour or boring cuts can achieve higher precision in pilot hole finishing.
Use of Thread Mills: Utilizing carbide thread mills for threading holes can avoid chip blockage and achieve high-precision thread machining.
Use of Minimal Quantity Lubrication (MQL): In thread machining, taps or thread mills with internal coolant holes can inject small amounts of lubricating oil onto the inner hole surface via compressed air, providing both lubrication and chip evacuation.
4. Common Problems in Tapping Aluminum Alloys
Aluminum alloys are generally soft and have good material characteristics, but due to their low melting point and high ductility, they tend to weld onto the surface of the tool during finishing. When using a tap designed for standard steel machining, the insufficient rake angle of the cutting edge can lead to weld formation at the tool tip, increasing machining difficulty. Furthermore, built-up edge can degrade surface roughness and machining accuracy.
Control of Cutting Temperature: Cutting temperature should be minimized as much as possible. This can be achieved by increasing the surface roughness of the front face of the tool to facilitate smooth chip evacuation or by using taps with internal cooling channels to provide minimal quantity lubrication, ensuring proper lubrication and cooling.
Using Forming Taps for Machining: Forming taps, designed for plastic deformation (extrusion processing), can help avoid weld formation on the cutting edge and prevent tap breakage.
Use of Thread Mills for Machining: Thread mills, capable of finely breaking and evacuating chips, are suitable for machining aluminum alloys. Combined with minimal quantity lubrication, they allow for high-speed cutting, which is one of their advantages. Currently, the use of environmentally friendly MQL for threading is increasing, and internal coolant taps are particularly effective in minimal quantity lubrication processing.
Leave a comment