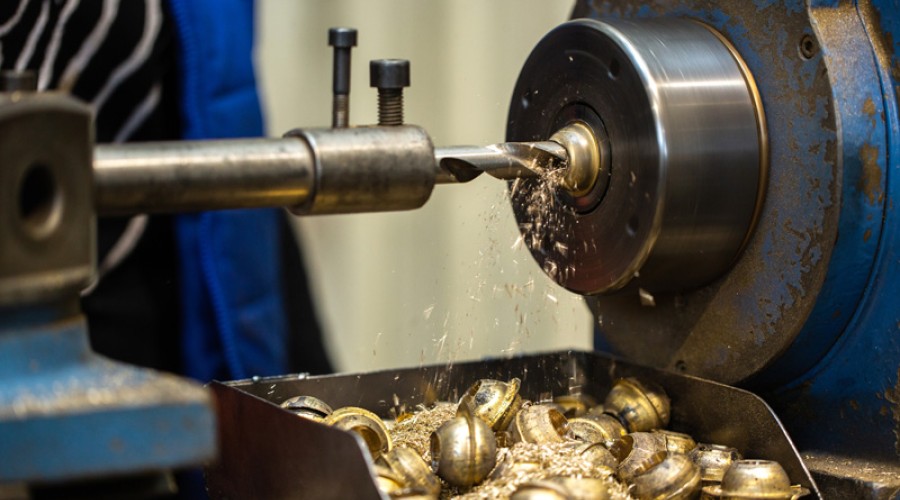
Machining Fundamentals Part 1: Mastering the Basic Operations and Applications of Conventional Lathe
I. What is Machining Process?
The process of altering the dimensions or properties of a workpiece using machining machinery.
1.1 Classification by Processing Method
Based on the temperature state of the workpiece during processing, it can be categorized as follows:
Cold Processing: Typically done at room temperature and does not cause chemical or phase changes in the workpiece; cold processing is divided into cutting and pressure processing.
Hot Processing: Generally carried out at temperatures above or below room temperature, causing chemical or phase changes in the workpiece; common methods include heat treatment, forging, casting, and welding.
1.2 Classification by Forming Method
Additive Manufacturing: Includes casting, forging, injection molding, powder forming, 3D printing, etc.
Subtractive Manufacturing: Includes turning, milling, drilling, planing, boring, grinding (surface grinding, cylindrical grinding, internal grinding, centerless grinding), CNC, EDM, wire cutting (slow wire, fast wire), welding (TIG, resistance welding, friction welding), laser processing (cutting, welding, marking), etching, etc.
II. Common Machining Equipment
Includes milling machines, drilling machines, boring machines, grinding machines, gear cutting machines, planers, spark machines, saw machines, wire cutting, engraving machines, laser cutting machines, precision engraving machines, CNC bending machines, etc.
Conventional Lathe
Equipment Overview
A lathe primarily uses a cutting tool to turn a rotating workpiece.
Common Processing Types
Turning face ends, external cylinders, boring holes, drilling holes, reaming holes, tapping holes, external/internal threading, cutting external/internal grooves, end face grooving, cylindrical knurling, taper turning, form turning, coaxial jig turning, copy turning, surface turning.
Processing Accuracy
The typical accuracy of turning is between IT7 and IT8, with a surface roughness of Ra0.8 to 1.6um.
Rough Turning
Aims to maintain cutting speed while using large cutting depths and feed rates to improve turning efficiency, though the accuracy only reaches IT11, with surface roughness of Ra10 to 20um.
Semi-Finishing and Finishing
Typically involves high speed with smaller feed rates and cutting depths, achieving accuracies between IT10 and IT7, with surface roughness from Ra0.16 to 10um.
Mirror Finishing
Using finely polished diamond cutting tools on high-precision lathes to perform high-speed precision turning of non-ferrous metals, achieving accuracies between IT5 and IT7, and surface roughness from Ra0.01 to 0.04um.
Processing Materials
Includes carbon steel, brass, stainless steel, alloy steel, aluminum alloys, zinc alloys, POM, plastics, acrylic, PE-UHWM (ultra-high molecular weight polyethylene), etc.
Leave a comment