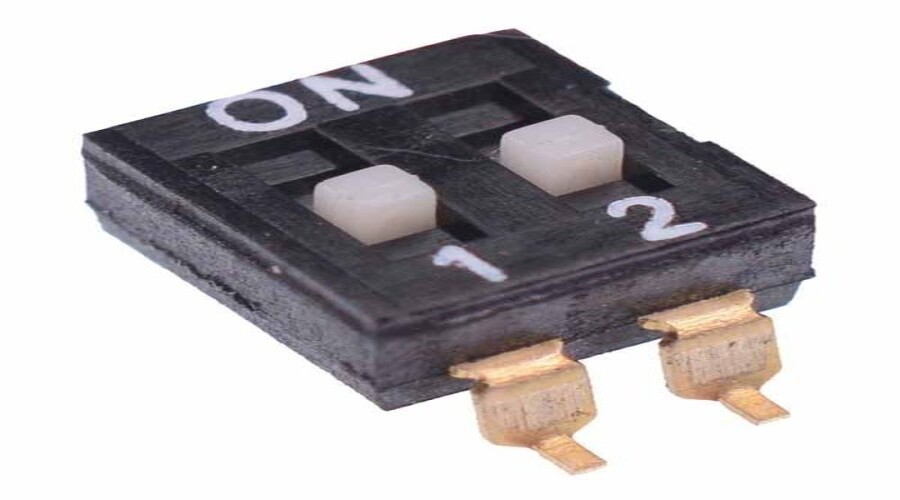
Amid the rush toward miniaturized electronics, the dip package style is staging a quiet revolution. This iconic through-hole design, once considered outdated, now bridges vintage durability with contemporary engineering needs. Discover how embracing DIP’s tactile advantages can unlock unexpected efficiencies in your workflows.
The Resurgence of DIP Aesthetics
1. Tangible Troubleshooting: The visible leads and socket-compatible dip package style simplify debugging—no X-ray machines or microscopic tools are required.
2. Hybrid Design Flexibility: Combine DIP-mounted microcontrollers with modern SMD peripherals for modular, upgrade-friendly systems.
3. Sustainability Edge: Reusable DIP sockets reduce e-waste compared to disposable surface-mount boards.
Hidden Opportunities in Plain Sight
Engineers are rediscovering dip package style applications beyond nostalgia:
· DIY Robotics: Prototype actuators and sensors using breadboard-friendly DIP components.
· Industrial Retrofit Kits: Maintain legacy machinery by swapping obsolete ICs with pin-compatible DIP upgrades.
· Art-Tech Installations: Creatives use DIP’s geometric layouts as visual design elements in interactive exhibits.
Future-Proofing Your DIP Strategy
Maximize ROI from dip package style adoption by:
1. Partnering with manufacturers offering tin-plated contacts (resists oxidation better than standard alloys)
2. Implementing conformal coating for moisture resistance in outdoor IoT deployments
3. Stocking DIP-format EEPROMs for field-reprogrammable firmware updates
The dip package style defies its "old-school" label by solving new problems—from sustainable prototyping to mixed-era system integration. In an era of disposable tech, DIP’s tactile, repairable design philosophy offers both functional and strategic advantages. Isn’t it time your designs embraced this enduring icon?
Leave a comment