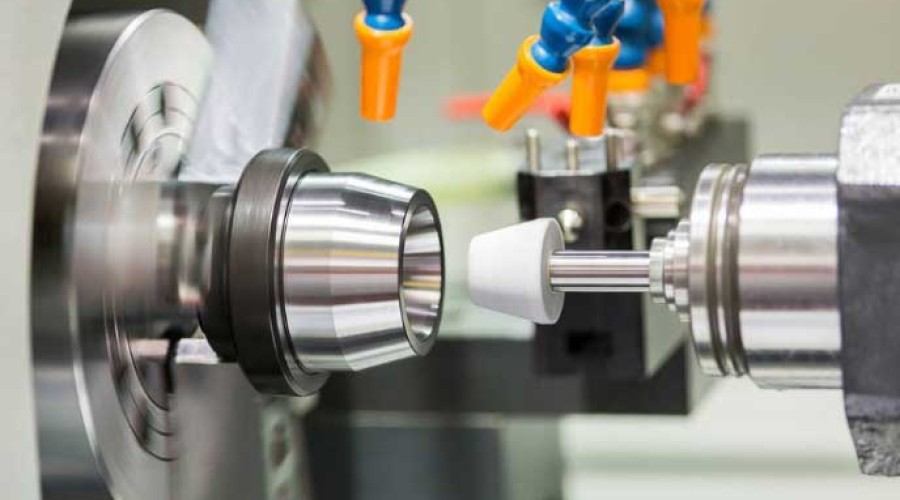
Introduction:
Machining is a fundamental process in modern manufacturing, serving as the cornerstone for the production of intricate components across various industries. This article provides a comprehensive exploration of machining, delving into its principles, techniques, and diverse applications that contribute to the creation of precise and complex parts.
1. Understanding Machining:
Machining refers to the subtractive manufacturing process where material is removed from a workpiece to achieve desired shapes, dimensions, and surface finishes. This process is crucial for producing components that meet stringent tolerances and quality standards, making it an integral part of industries such as aerospace, automotive, medical, and electronics.
2. Types of Machining Processes:
Turning:
In turning operations, a workpiece rotates
on a spindle, and a cutting tool removes material to create cylindrical shapes.
This process is commonly used for producing shafts, cylinders, and other
rotational parts.
Milling:
Milling involves a rotating cutting tool
that moves along multiple axes to remove material from the workpiece. It is
versatile, allowing for the creation of a wide range of shapes, including
slots, pockets, and complex contours.
Drilling:
Drilling is the process of creating holes
in a workpiece using a rotating cutting tool. It is a fundamental operation in
machining and is employed in various industries for component assembly.
Grinding:
Grinding is a precision machining process
where abrasive particles are used to remove material from a workpiece. It is
employed for achieving tight tolerances and fine surface finishes, making it
vital in tool and die manufacturing.
Electrical Discharge Machining (EDM):
EDM uses electrical discharges to remove
material from a workpiece. It is particularly useful for machining complex
shapes and hardened materials that are challenging to machine using traditional
methods.
3. CNC Machining:
Computer Numerical Control (CNC) machining has revolutionized the precision and efficiency of traditional machining processes. CNC machines are equipped with computer-controlled systems that automate tool movements, allowing for highly accurate and repeatable operations. This technology is prevalent in turning, milling, and drilling applications, offering versatility and flexibility in producing complex components.
4. Precision and Tolerances:
Machining is synonymous with precision, and achieving tight tolerances is a hallmark of this manufacturing process. Tolerances refer to the permissible limits of variation in a part's dimensions, ensuring that the final product meets design specifications. Precision machining is essential in industries like aerospace and medical, where components must adhere to strict tolerances for safety and functionality.
5. Materials in Machining:
Machining is performed on a wide range of materials, including metals, plastics, ceramics, and composites. Each material presents unique challenges and considerations in terms of tool selection, cutting speeds, and feed rates. Advanced machining techniques and tools have been developed to address the specific characteristics of different materials, enabling the production of high-quality components.
6. Applications in Various Industries:
Aerospace:
Machining is integral to aerospace
manufacturing, where lightweight and high-strength materials are used to
produce components such as aircraft parts and turbine blades.
Automotive:
The automotive industry relies on machining
for the production of engine components, transmission parts, and various
precision-machined elements that contribute to vehicle performance and safety.
Medical:
In the medical field, machining is used to
manufacture implants, surgical instruments, and medical devices with intricate
geometries, demanding the highest levels of precision.
Electronics:
Machining is essential in electronics
manufacturing for producing components like circuit boards, connectors, and
housings with tight tolerances to ensure functionality and reliability.
7. Challenges and Innovations:
Despite its essential role, machining faces challenges such as tool wear, heat generation, and material-specific difficulties. Innovations in cutting tool materials, coatings, and machining strategies continue to address these challenges, pushing the boundaries of what is achievable in terms of speed, precision, and sustainability.
Conclusion:
Machining stands as a cornerstone in the
intricate tapestry of modern manufacturing, where precision and efficiency are
non-negotiable. From turning and milling to CNC machining and EDM, the diverse
techniques and applications of machining have transformed industries and
propelled technological advancements. As manufacturing continues to evolve,
machining remains an indispensable process, shaping the way intricate
components are brought to life across a myriad of sectors.
Leave a comment