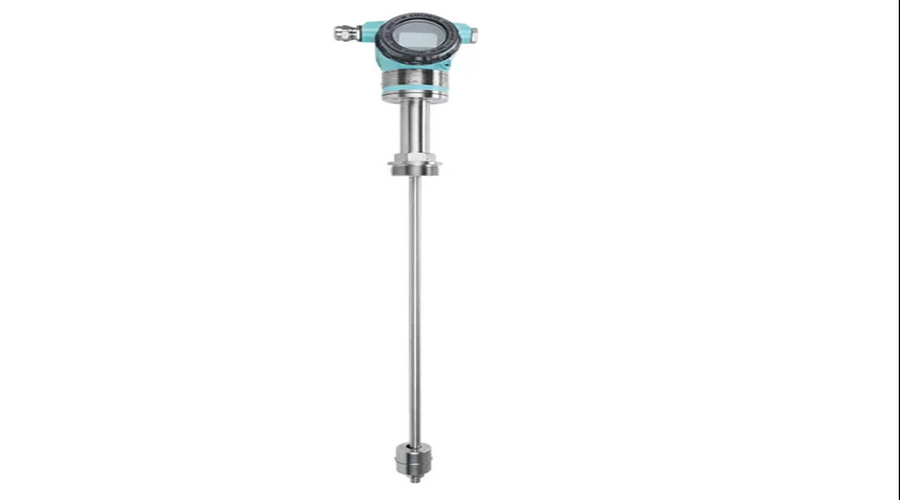
Magnetostriction is a physical phenomenon where certain ferromagnetic materials (e.g., iron, nickel, cobalt, and their alloys) undergo slight shape changes (expansion, contraction, or twisting) when exposed to a magnetic field. Conversely, mechanical stress on these materials can alter their magnetic properties. This two-way effect is key to its applications in sensors.
Core Mechanism
Direct Magnetostriction:
- When a magnetic field is applied, the material’s internal magnetic domains (tiny magnetic regions) realign, causing a measurable physical deformation.
- Example: A nickel rod slightly elongates in a magnetic field and returns to its original length when the field is removed.
Inverse Magnetostriction (Villari Effect):
- Applying mechanical stress (e.g., pressure or strain) to the material changes its magnetic state, which can be detected as a magnetic signal.
- Example: Squeezing a magnetostrictive rod generates a detectable change in its surrounding magnetic field.
Application in Sensors
Magnetostrictive level sensors use the inverse magnetostriction effect to measure liquid levels:
- A magnetostrictive waveguide wire (e.g., iron-cobalt alloy) runs through the sensor.
- A float (with a permanent magnet) moves along the wire as the liquid level changes.
- A current pulse sent through the wire creates a magnetic field that interacts with the float’s magnet, generating a torsional stress wave in the wire.
- The sensor calculates the liquid level by measuring the time it takes for the stress wave to travel from the float to the detector.
Advantages & Limitations
- Pros: High accuracy (±0.5 mm), non-contact measurement, resistance to extreme temperatures/pressures, and strong immunity to interference.
- Cons: Higher material costs (e.g., Terfenol-D alloy), sensitivity to strong external magnetic fields.
Common Materials: Terfenol-D (terbium-dysprosium-iron alloy), nickel-iron ferrites.
Leave a comment