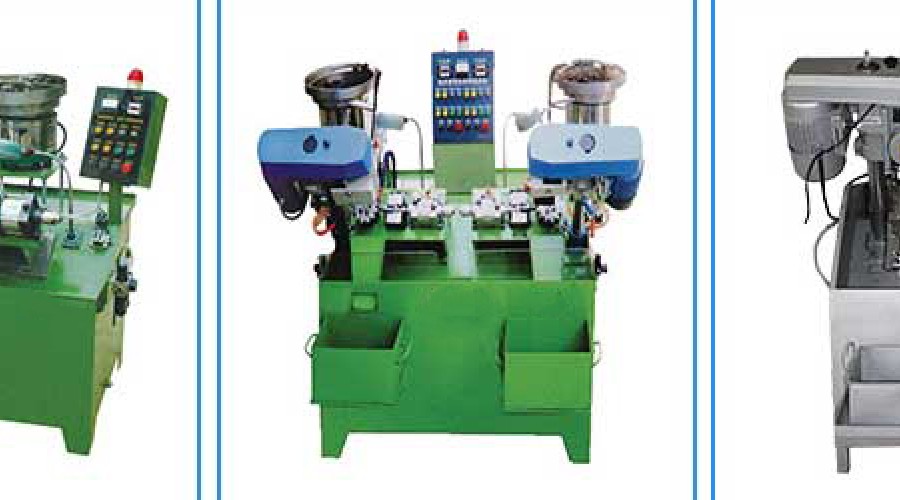
Introduction:
In the realm of manufacturing, the efficiency and precision of fastener production are crucial for a wide range of industries. Nut tapping machines emerge as essential tools in this process, offering unique capabilities that streamline production, enhance quality, and contribute to the overall efficiency of assembly operations. This article explores the applications of nut tapping machines, shedding light on their diverse uses and impact in modern manufacturing.
1. Understanding Nut Tapping Machines:
Nut tapping machines are specialized equipment designed for threading nuts by creating internal threads. This process, known as tapping, involves the use of a tapping tool to cut threads into the interior of a nut, enabling it to be securely fastened onto a bolt or screw. Nut tapping machines are capable of performing this operation rapidly and precisely, making them indispensable in various manufacturing settings.
2. Mass Production of Threaded Nuts:
One of the primary applications of nut tapping machines lies in the mass production of threaded nuts. These machines can efficiently and consistently create internal threads in a large volume of nuts, ensuring uniformity and adherence to tight tolerances. Industries such as automotive manufacturing and construction rely on the speed and reliability of nut tapping machines to meet the demands of high-volume production.
3. Automotive Industry:
In the automotive sector, where precision and efficiency are paramount, nut tapping machines play a critical role in producing threaded nuts for various components. From suspension systems to engine components, the use of nut tapping machines ensures that threaded connections are standardized and meet the rigorous quality standards of the automotive industry.
4. Aerospace Applications:
In the aerospace industry, where safety and precision are non-negotiable, nut tapping machines contribute to the production of threaded nuts used in critical components of aircraft. These machines provide the necessary precision to create reliable threaded connections that withstand the demanding conditions of aerospace applications.
5. Customization for Specialized Fasteners:
Nut tapping machines can be customized to create specialized or non-standard threaded nuts. This flexibility allows manufacturers to meet specific design requirements and produce fasteners tailored to unique applications. Industries with specialized needs, such as electronics and medical device manufacturing, benefit from the ability to create custom threaded nuts using these machines.
6. Increased Production Speed and Efficiency:
The automation and speed of nut tapping machines significantly increase production efficiency. These machines can rapidly tap multiple nuts in a continuous process, reducing cycle times and increasing overall output. This enhanced efficiency is particularly advantageous in industries where production speed is a critical factor in meeting market demands.
7. Improved Thread Quality:
Nut tapping machines contribute to the improvement of thread quality in threaded nuts. The precision and consistency of the tapping process result in threads with accurate dimensions and minimal defects. This is essential for ensuring the reliability and longevity of fastened connections, particularly in applications where safety and durability are paramount.
8. Versatility in Material Compatibility:
Nut tapping machines are designed to work with a variety of materials, including metals, plastics, and composites. This versatility allows manufacturers to produce threaded nuts for diverse applications across different industries. Whether it's creating threaded nuts for steel structures or lightweight components in electronics, nut tapping machines adapt to the material requirements of the specific application.
Conclusion:
Nut tapping machines stand at the forefront
of fastener production, providing a seamless and efficient solution for
creating threaded nuts. From mass production in automotive assembly lines to
the precision demands of the aerospace industry, these machines contribute to
the reliability and efficiency of threaded connections in various sectors. As
manufacturing continues to evolve, nut tapping machines remain pivotal tools,
driving advancements in threaded fastener production and supporting the demands
of diverse industries.
Leave a comment