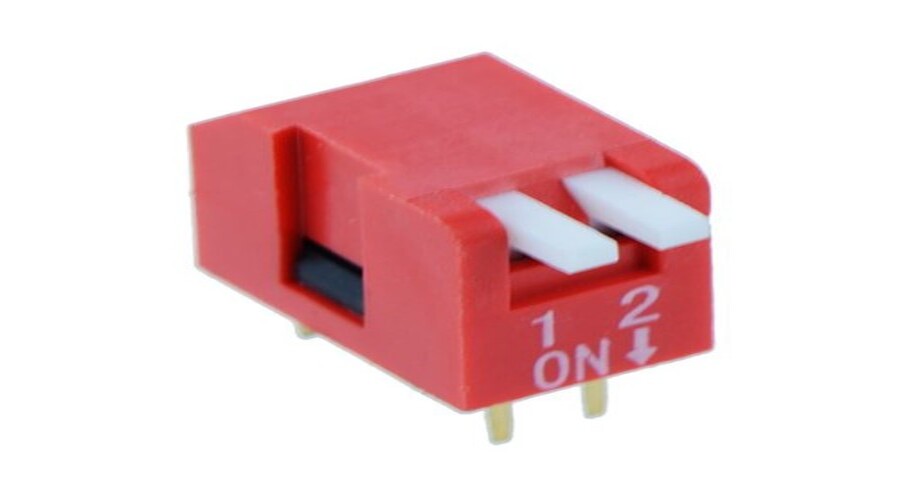
In today’s fast-paced electronics industry, the dip package remains a cornerstone for reliable circuit integration. While flashy innovations dominate headlines, this decades-old packaging solution quietly powers everything from industrial controllers to consumer gadgets. Let’s explore why engineers still rely on DIP technology—and how it can elevate your next project.
Why the DIP Package Still Matters
1. Simplified Prototyping: Unlike surface-mount alternatives, dual in-line packages (DIP) enable quick manual soldering, reducing development time for small-batch projects.
2. Enhanced Thermal Stability: The elongated leads in DIP designs dissipate heat more effectively than compact ICs, minimizing failure risks in high-temperature environments.
3. Cost-Effective Repairs: Replace faulty components without specialized tools—a critical advantage for legacy systems or budget-conscious teams.
Applications You Might Overlook
Beyond classic computing boards, dip packages shine in niche sectors:
· Retro-tech restoration: Vintage synthesizers and arcade machines often require DIP-compatible ICs.
· Educational kits: Universities favor DIP components for hands-on engineering courses.
· Custom IoT modules: Hobbyists leverage DIP sockets for rapid sensor integration.
Choosing the Right DIP Partner
When sourcing dip package solutions, prioritize suppliers offering:
· MIL-STD-883 compliance for military-grade durability
· Lead-free options meeting RoHS 3 standards
· Custom pin-count configurations (16–40 pins)
The dip package isn’t just a relic—it’s a flexible tool adapting to modern engineering challenges. By combining proven reliability with surprising versatility, this packaging format continues to solve problems that newer technologies can’t address. Ready to optimize your designs with DIP’s unique advantages? Your next breakthrough might hinge on this humble hero.
Leave a comment