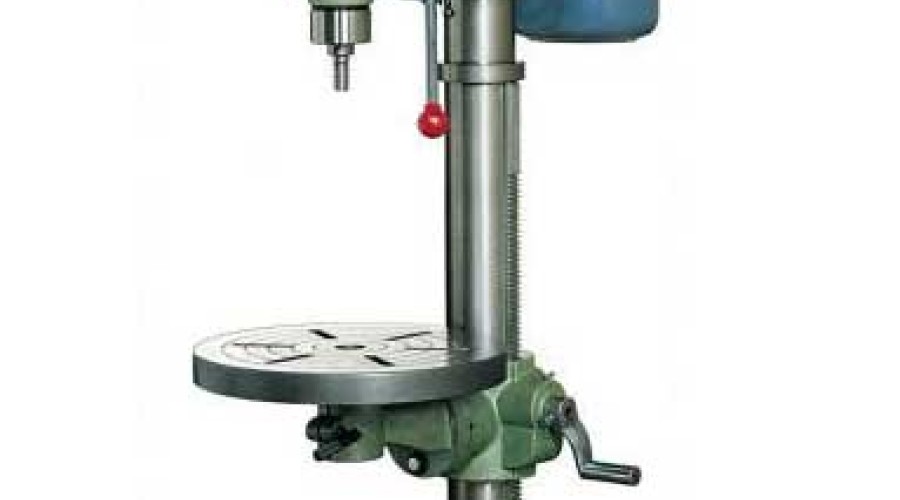
Automatic drillingmachines have played a pivotal role in revolutionizing manufacturing processes,
offering unparalleled precision, efficiency, and cost-effectiveness. These
machines have come a long way from their early iterations, transforming the
landscape of industries that rely on drilling operations. In this article, we
will explore the evolution of automatic drilling machines, their key features,
and the impact they have had on various sectors.
The concept of automatic drilling dates back to the industrial revolution, with early machines driven by steam engines. These machines were characterized by basic automation, allowing operators to perform repetitive drilling tasks with increased speed and consistency. Over time, as electricity became more prevalent, automatic drilling machines transitioned to electric power, paving the way for further advancements.
Computer Numerical Control (CNC) Technology: One of the most significant advancements in automatic drilling machines is the integration of CNC technology. CNC allows for precise control of the drilling process by utilizing computer programs to dictate the movement and speed of the drill. This results in unparalleled accuracy and repeatability, reducing the likelihood of errors and minimizing material waste.
Multi-Axis
Capability: Modern automatic drilling machines often feature multi-axis
capabilities, enabling them to move in multiple directions simultaneously. This
flexibility is crucial for drilling complex patterns and intricate designs,
meeting the demands of diverse industries such as aerospace and automotive
manufacturing.
Automated Tool
Changing: To enhance efficiency and reduce downtime, automatic drilling
machines are equipped with automated tool-changing systems. These systems
enable the machine to switch between different drill bits or tools seamlessly,
allowing for the drilling of multiple hole sizes and types in a single
operation.
Sensors and Feedback Systems: Advanced sensors and feedback systems are integrated into automatic drilling machines to monitor and adjust parameters in real-time. These systems ensure consistent performance, detecting variations in material hardness, tool wear, or any anomalies that could affect the drilling process. Automatic adjustments based on these inputs contribute to improved efficiency and product quality.
Integration with
Industry 4.0: In the era of Industry 4.0, automatic drilling machines are
becoming interconnected through the Internet of Things (IoT). This connectivity
enables real-time monitoring, data collection, and analysis, facilitating
predictive maintenance and optimizing the overall manufacturing process.
Aerospace:
Automatic drilling machines have become indispensable in aerospace
manufacturing, where precision is paramount. The ability to drill intricate
patterns and holes with high accuracy ensures the production of lightweight yet
durable components, contributing to the overall efficiency and safety of
aircraft.
Automotive: In the
automotive industry, automatic drilling machines play a crucial role in the
production of chassis components, engine parts, and body structures. The speed
and precision of these machines contribute to the mass production of vehicles
while maintaining quality standards.
Construction: Automatic drilling machines are employed in the construction industry for tasks such as drilling holes in concrete or steel structures. Their efficiency and accuracy enhance construction processes, leading to faster project completion and reduced labor costs.
The evolution of automatic drilling machines has been marked by technological advancements that continue to redefine manufacturing processes across various industries. From basic automation to the integration of CNC technology and Industry 4.0, these machines have come a long way, offering precision, efficiency, and versatility. As technology continues to advance, we can expect further innovations that will push the boundaries of what automatic drilling machines can achieve, contributing to the ongoing transformation of the manufacturing landscape.
Leave a comment