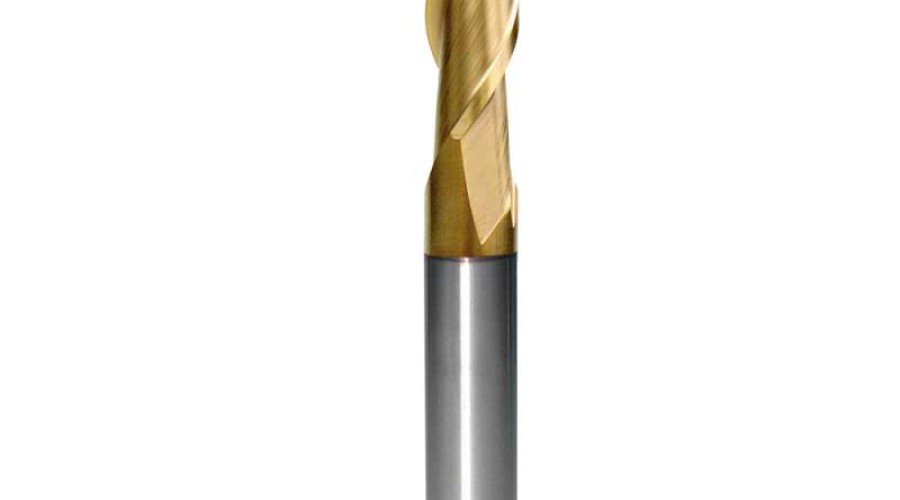
Considering factors such as cutting efficiency, tool life, and the shape of the workpiece, it is almost impossible to complete all machining tasks with a single tool. The most commonly used tools can be divided into the following three categories:
1.End Mills: These have cutting edges on the outside edge and the bottom, forming two machinable planes at a 90-degree angle, without an R (radius) corner.
- Advantages: They are well-suited for machining flat surfaces (bottom or side), such as 2D shapes like face milling, slot milling, and contour milling.
- Disadvantages: When used for 3D shapes, the lack of an R corner transition makes the tool very brittle, leading to easy breakage and unstable tool life. Additionally, due to the sharp corners, when machining 3D shapes, only a limited amount of material can be cut at a time. To achieve the desired machining effect, the tool spacing and cutting depth must be reduced, resulting in lower machining efficiency.
2.Ball Nose Mills: These have a large R corner equivalent to the tool's radius, forming a spherical cutting edge shape.
- Advantages: The cutting edge with a large R corner is stronger than the sharp corners of an end mill, making it less prone to breakage and providing more stable tool life. Moreover, when used for 3D machining, the area cut by the ball nose mill is the R-corner cutting edge, allowing for larger stepovers and cutting depths, which increases machining efficiency and improves the surface quality.
- Disadvantages: When using a ball nose mill for 3D shapes, the contact point between the cutting edge and the workpiece constantly changes, leading to unstable cutting speeds. As shown in the diagram, at positions a and c, the cutting speed is stable, resulting in a good machined surface. However, at positions b and d, the cutting speed is very low or even non-existent, causing the cutting edge to effectively rub against the workpiece, which can affect surface quality. The bottom of the ball nose mill is rounded, which limits its cutting range and makes it prone to wear, reducing machining precision, especially when working on relatively flat surfaces.
3.Bull Nose Mills: These combine the advantages of end mills and ball nose mills, with a small R corner on the edge while retaining the cutting function of the bottom cutting edge. Essentially, they are end mills with an R corner that is smaller than the tool's radius.
- Advantages: When milling similar workpieces, the bull nose mill can maintain a consistent cutting speed at all four points, resulting in better surface quality than a ball nose mill. Additionally, since it retains the bottom cutting ability of the end mill, it can achieve relatively fast milling speeds when machining flatter surfaces.
Leave a comment