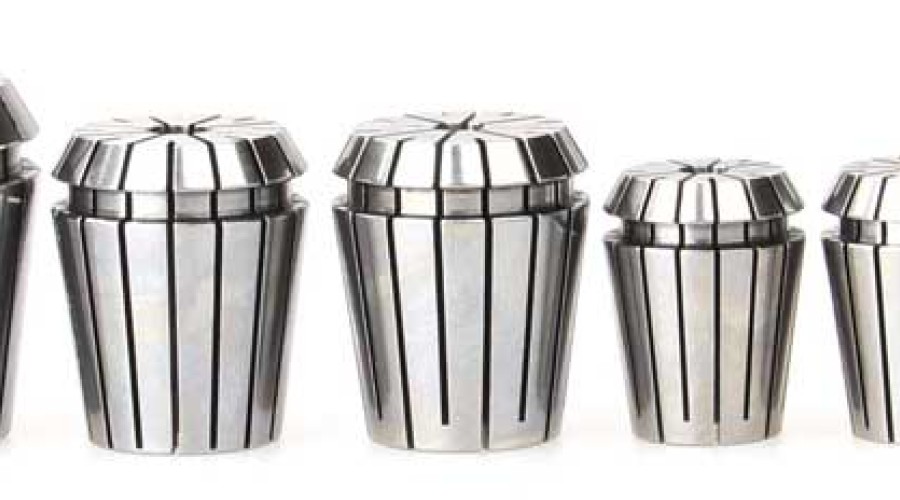
ER collets are a versatile and widely used tool in machining, CNC (Computer Numerical Control) machines, and engraving machines. Among the ER series, the ER32 collet stands out due to its dimensions and versatility. This article will provide a detailed overview of the ER32 collet dimensions and their applications.
What is an ER32 Collet?
The ER32 collet is a type of elastic collet, originally invented by the German company Rego-Fix and widely adopted globally. It consists of the collet body and a collet nut, offering high precision, strong clamping force, and excellent repeatability. ER32 collets are ideal for clamping various tools and workpieces, making them a staple in CNC machining centers and engraving machines.
Key Dimensions of ER32 Collets
ER32 collets have standardized dimensions, ensuring compatibility with various spindle and tool holder brands. Here are the main dimensions of the ER32 collet:
Clamping Range:
- 2mm to 20mm (or 1/16" to 13/16")
Collet Length (L):
- 40mm
Collet Diameter (D):
- Maximum Outer Diameter: 33mm
- Taper Angle: 8°
Clamping Accuracy:
- Standard Accuracy: 0.015mm
- High Precision: 0.005mm
Thread Size:
- ER32 collets typically use M32 x 1.5 thread size for securing in the collet chuck.
Applications of ER32 Collets
ER32 collets are widely used in various machining applications, including:
Tool Holding:
- ER32 collets can hold various types of tools such as drill bits, end mills, boring bars, and taps. Their high precision and strong clamping force ensure tool stability and accuracy during machining.
Workpiece Clamping:
- In specific machining scenarios, ER32 collets can also be used to hold small workpieces or those requiring high-precision positioning.
Engraving and CNC Machines:
- In engraving and CNC machines, ER32 collets are commonly used to hold engraving tools and machining tools, ensuring efficient and precise processing.
Choosing and Maintaining ER32 Collets
Choosing ER32 Collets
When selecting the appropriate ER32 collet, consider the following factors:
- Machining Requirements: Choose the suitable clamping range and precision based on your specific machining needs.
- Collet Material: High-quality ER32 collets are usually made from premium steel, offering longer service life and better clamping performance.
- Brand and Compatibility: Opt for reputable brands to ensure compatibility with your existing equipment.
Maintaining ER32 Collets
- Regular Cleaning: Clean the collet and collet holder regularly after use to prevent debris and chips from accumulating.
- Lubrication: Lubricate the collet periodically to ensure smooth operation and durability of the moving parts.
- Wear Inspection: Check for wear and tear regularly, and replace any damaged or less accurate collets promptly.
Leave a comment