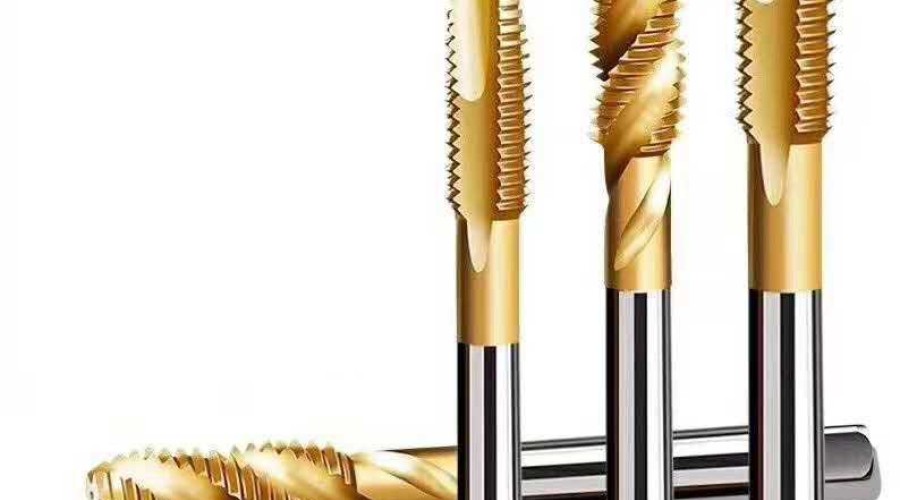
A tap is a tool used to process internal threads. According to its shape, it can be divided into spiral groove taps, helix angle taps, straight groove taps, and pipe taps. According to the usage environment, it can be divided into hand taps and machine taps. According to the specifications, it can be divided into metric, American, and British taps, etc. Taps are the most mainstream processing tools used by operators in the manufacturing industry when tapping. Today, the editor will take you to understand tapping and master tapping!
01.What is tapping
Tapping is the process of using a certain torque to rotate the tap into the bottom hole to be drilled to process internal threads. The process of making internal threads is called tapping, and its tool is called a tap.
02.Key Points
(1) The aperture of the threaded bottom hole on the workpiece should be chamfered, and both ends of the through hole thread should be chamfered.
(2) The clamping position of the workpiece should be correct, and the centerline of the threaded hole should be placed horizontally or vertically as much as possible, so that it is easy to determine whether the tap axis is perpendicular to the plane of the workpiece.
(3) At the beginning of tapping, try to align the tap properly, then apply pressure to the tap and rotate the handle. When cutting 1-2 turns, carefully check and correct the position of the tap. When cutting 3-4 turns of thread, the position of the tap should be correct. After that, only rotate the handle without applying pressure to the tap, otherwise the thread teeth will be damaged.
(4) When tapping, every half to one turn of the handle should be reversed by about half a turn to facilitate the breaking and discharge of the chips, and reduce the phenomenon of the tap getting stuck due to chip adhesion.
(5) When encountering a tapped hole that cannot be tapped through, the tap should be withdrawn frequently to remove the chips in the hole.
(6) When tapping plastic materials, lubricant cooling fluid should be added. For steel materials, general-purpose machine oil or higher concentration emulsion is used, and higher requirements can use vegetable oil or molybdenum disulfide, etc. For stainless steel, No. 30 machine oil or sulfurized oil can be used.
(7) When switching to the next tap during tapping, first screw it into the threaded hole that has been tapped by hand until it cannot be screwed in further, and then use the handle to turn it. When withdrawing the taper tap at the end of tapping, avoid rapid rotation of the handle, and it is best to screw it out by hand to ensure that the quality of the threaded hole that has been tapped is not affected.
(8) During machine tapping, the tap and the threaded hole should maintain coaxiality.
(9) During machine tapping, the calibration part of the tap cannot all protrude, otherwise, disorderly teeth will occur when the tap is reversed during retraction.
(10) The cutting speed during machine tapping is generally 6-15 meters/min for steel, 5-10 meters/min for quenched and tempered steel or harder steel, 2-7 meters/min for stainless steel, and 8-10 meters/min for cast iron. For taps with the same material, take higher values for smaller tap diameters and lower values for larger tap diameters.
03.Rigid tapping
Also known as "synchronous feed tapping," rigid tapping synchronizes spindle rotation with feed to match specific thread pitches. Because the feed into the hole is synchronized, theoretically, no integral tap holders with any tension compression should be used.
However, the problem that exists in practical production is that the machine tool cannot precisely match the specific tap pitch being used. There is always a slight difference between the threads processed by the machine tool and the actual pitch of the tap. If an integral tap holder is used, this difference will have a decisive impact on the tap life and thread quality because additional axial forces need to be applied to the tap.
If a tension-compression floating tap holder is used, the tap life and thread quality will be greatly improved because the additional axial forces on the tap are eliminated. The problem with traditional tension-compression tap holders is that they cause significant changes in thread depth. As the tap becomes dull, the pressure required to start the tap into the hole increases, and the compression stroke used in the tap driver before the tap begins cutting is greater. As a result, the tapping depth is shallower.
One of the main advantages of rigid tapping is the ability to accurately control the depth in blind hole machining. To precisely and consistently process workpieces, tap holders with sufficient compensation need to be used to achieve higher tap life without causing any changes in depth control.
Specialized lubricants are also needed for tapping operations, which can effectively reduce friction between the workpiece and tap, reduce wear, provide a tough oil film to prevent surface scratches and wrinkles on the workpiece, and improve work quality and efficiency. They also suppress temperature rise, reduce the generation of sintering and jamming, prolong the life of the tooling, protect the tools, inhibit the generation of black sludge, and do not corrode the workpiece; with remarkable cooling effects.
It is important to choose the right lubricant for tapping operations. For applications where cleaning is not required, a self-cleaning tapping lubricant should be used. For difficult-to-machine workpieces, pure oil-based tapping oil is required.
04.Factors affecting tapping
1>.Tapping equipment
- Machine tool: It can be divided into vertical and horizontal processing methods. For tapping, vertical processing is preferred over horizontal processing, and when processing horizontally, consideration should be given to whether the cooling is sufficient.
- Tap holder: It is recommended to use a dedicated tap holder for tapping, and for machine tools with good rigidity and stability, priority should be given to using synchronous tapping holders. Conversely, flexible tapping holders with axial/radial compensation should be used as much as possible. Except for small-diameter taps (
- Cooling conditions: For tapping, especially for extrusion taps, the requirement for coolant is lubrication > cooling; in actual use, it can be adjusted according to the machine tool conditions (when using emulsion, it is recommended that the concentration be greater than 10%).
2>.Workpiece being machined
Material and hardness of the workpiece: The hardness of the workpiece material should be uniform, and it is generally not recommended to use taps to process workpieces with a hardness exceeding HRC42.
Tapped hole: Hole structure, selection of appropriate drills; hole size accuracy; hole wall quality.
3>.Machining parameters
Speed: The speed is determined based on the type of tap, material, hardness, the material being machined, and the quality of the tapping equipment. Usually, select according to the parameters given by the tap manufacturer.
The speed must be reduced under the following conditions:
- Poor machine tool rigidity; large tap runout; insufficient cooling;
- Uneven material or hardness in the tapping area, such as welds;
- The tap is extended, or an extension rod is used;
- Horizontal machining with external cooling;
- Manual operation, such as bench drills, radial drills, etc.
Feed: For rigid tapping, the feed rate is equal to 1 pitch/revolution. For flexible tapping, and when the tool holder compensation variable is sufficient: the feed rate is (0.95-0.98) pitches/revolution.
05.Tips for selecting taps
Tolerance of taps with different precision grades
Selection basis: The precision grade of taps cannot be determined solely based on the precision grade of the threaded workpiece.
1.1. Material and hardness of the workpiece being machined;
1.2. Tapping equipment (such as machine tool conditions, clamping tool holders, cooling environment, etc.);
1.3. Precision and manufacturing errors of the tap itself.
For example: When machining a 6H thread, a 6H precision tap can be used for steel workpieces; when machining gray cast iron, due to the faster wear of the tap's core diameter and the smaller amount of hole expansion, it is advisable to use a 6HX precision tap for better life.
Tap outer dimensions
- Currently, the most commonly used are DIN, ANSI, ISO, JIS, etc.;
- Choose the appropriate overall length, flute length, and shank size according to different machining requirements or existing conditions of customers;
- Interference during machining;
Six basic elements for tap selection
- Type of threaded processing, metric, imperial, American, etc.;
- Type of threaded hole, through hole or blind hole;
- Material and hardness of the workpiece being machined;
- Depth of the complete thread and depth of the bottom hole of the workpiece;
- Precision requirements for the workpiece thread;
- Standard shape of the tap.
Leave a comment