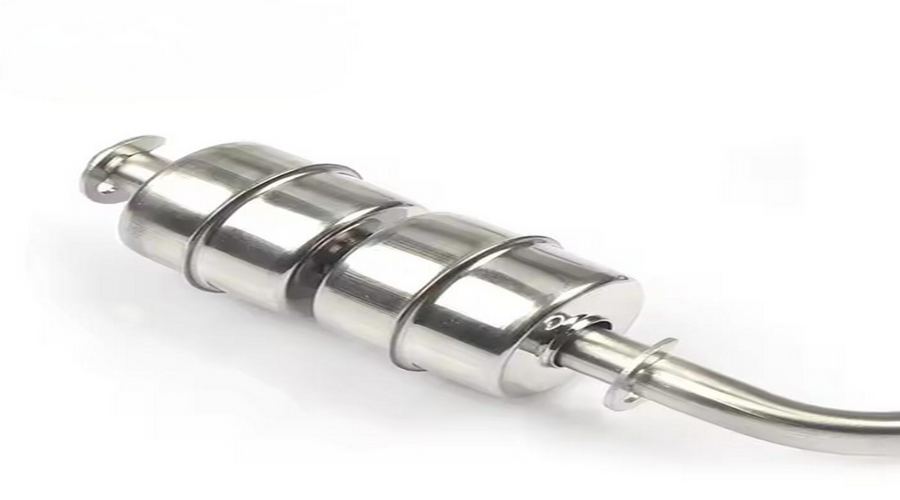
In a world where every drop counts, the water level sensor float switch emerges as the cornerstone of intelligent liquid control. Unlike generic alarms or error-prone digital systems, this device combines mechanical simplicity with sensor-grade accuracy to safeguard operations across industries. From preventing aquaculture tank overflows to optimizing pharmaceutical coolant loops, its role is as critical as it is invisible.
Why Traditional Liquid Detection Tools Fall Short
Many still rely on ultrasonic sensors that fail in foam-filled environments or conductive probes that corrode within months. The water level sensor float switch sidesteps these pitfalls through a gravity-driven design. A hermetically sealed magnetic reed switch pairs with a buoyant float, creating discrete activation points immune to liquid turbidity, temperature swings, or chemical exposure. This makes it the go-to choice for biodiesel reactors where glycerin byproducts coat other sensors or stormwater basins where floating debris tricks optical systems.
Industries Revolutionized by Float Switch Precision
· Smart Home Water Tanks: Automate refill cycles while preventing roof leaks through millimeter-level accuracy in IoT-connected cisterns.
· Food Processing Brine Systems: Maintain exact salinity bath depths during meat curing, eliminating human measurement errors.
· Hydropower Cooling Channels: Trigger emergency turbine shutdowns when water dips below minimum levels, avoiding $500k/minute damage risks.
Adaptive Alert Systems for Modern Needs
Today’s water level sensor float switch isn’t just a binary trigger—it’s a data hub. Advanced models integrate with SCADA systems, offering gradient alerts (e.g., 75% full, 90% critical) for proactive resource planning. In solar desalination plants, this enables operators to stagger water storage based on sunlight availability, cutting energy waste by 34%. For municipalities, predictive algorithms use float switch data to preempt pipe freeze risks during cold snaps.
Engineered for the Unforgiving
Standard sensors crumble in extreme conditions, but purpose-built water level sensor float switch variants thrive:
· Acid Mine Drainage Pits: Teflon-coated floats resist sulfuric acid concentrations up to 80%.
· Arctic Fuel Reservoirs: Sub-zero models with heated stems prevent ice-jam false alarms.
· High-Pressure Boilers: Reinforced switches handle 150 PSI steam environments without seal failure.
The Sustainability Multiplier
Water scarcity demands smarter usage. Agricultural co-ops using water level sensor float switch-controlled drip networks report 18% higher crop yields with 40% less water. In car washes, closed-loop systems guided by dual-stage float switches recycle 92% of runoff, slashing utility bills. Even data centers leverage these devices to cool servers using harvested rainwater, achieving LEED certification benchmarks.
Water Level Sensor Float Switch: Where Reliability Meets Affordability
Why gamble with complex, maintenance-heavy alternatives? This unassuming device delivers lab-grade monitoring at DIY-project pricing. Its fail-safe operation has become non-negotiable for disaster-prone areas—California wineries now install them in irrigation ponds to comply with drought laws, while offshore rigs use them as secondary leak detectors alongside $20k sonar units.
From microbreweries to nuclear cooling ponds, the water level sensor float switch isn’t just a tool—it’s your silent partner in resource mastery. Upgrade your liquid logic today.
Leave a comment