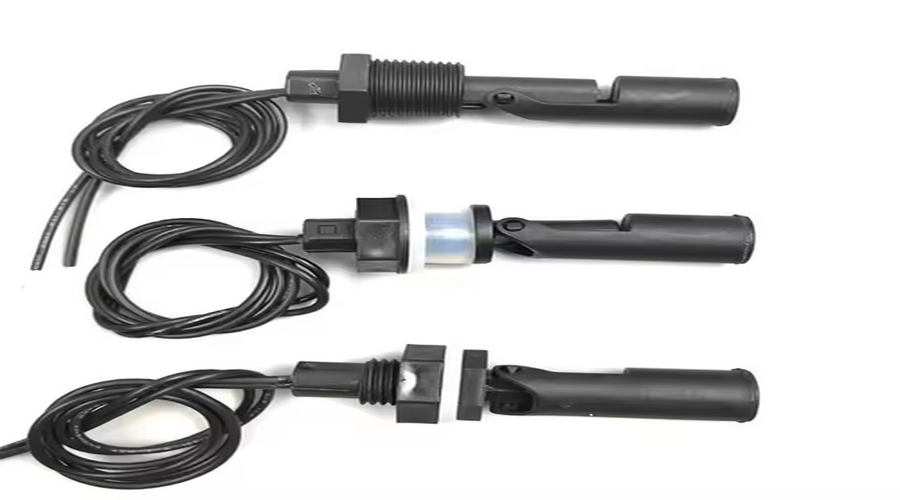
A float switch, often called a buoyancy-driven sensor, is a compact device engineered to monitor and regulate liquid levels in tanks, reservoirs, or pipelines. Leveraging simple mechanical principles—such as a buoyant component that rises or falls with fluid height—activates or deactivates connected equipment like pumps, alarms, or valves. This unassuming tool is a cornerstone in industries ranging from water treatment to food processing, where precise liquid management is nonnegotiable.
How Buoyant Sensors Operate: A Closer Look
This apparatus houses a sealed float attached to an arm or stem at its core. As liquid ascends, the buoyant unit lifts, tilting the arm to trigger an internal switch mechanism (e.g., a magnetic reed or microswitch). Conversely, dropping levels lower the float, breaking the circuit. In sump pumps, for example, a descending float might shut off the pump once a tank is emptied. This analog design thrives in environments where electronics fail, such as corrosive liquids or extreme temperatures.
Beyond Basics: Unexpected Roles in Modern Workflows
While preventing overflow or dry runs is its primary duty, buoyant sensors unlock efficiency in niche applications. Aquaculture systems use them to maintain oxygen-rich water levels, while breweries automate ingredient dosing during fermentation. Even renewable energy sectors rely on these devices to manage coolant flow in solar thermal installations. Their adaptability to diverse fluids—from oil to viscous slurries—makes them irreplaceable in custom industrial setups.
Leave a comment