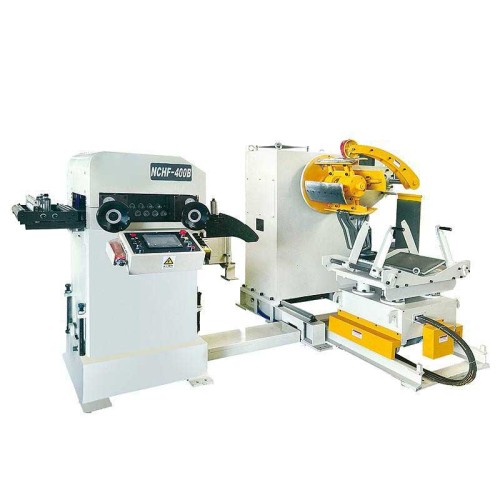
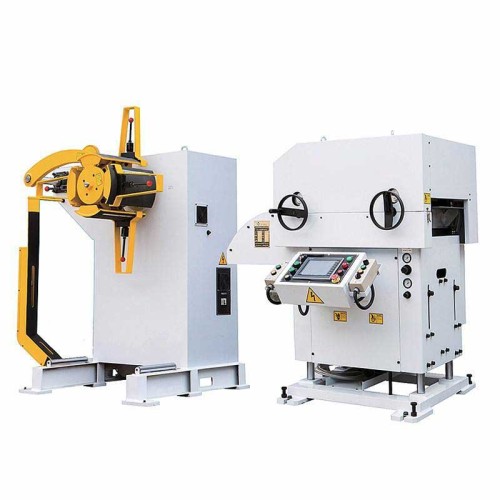
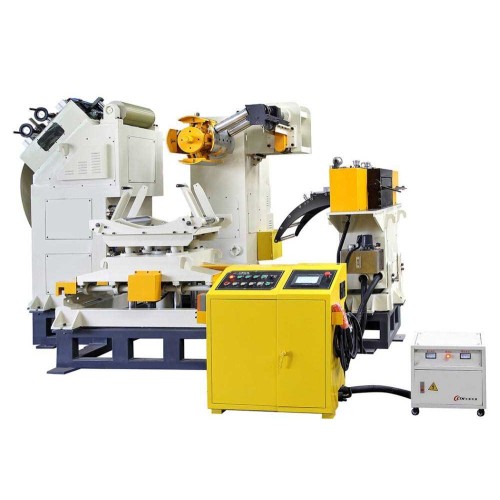
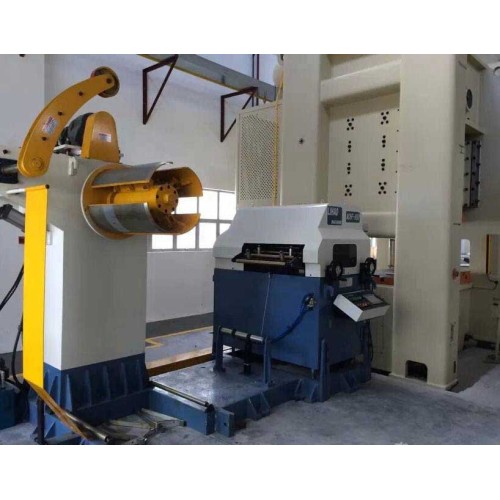
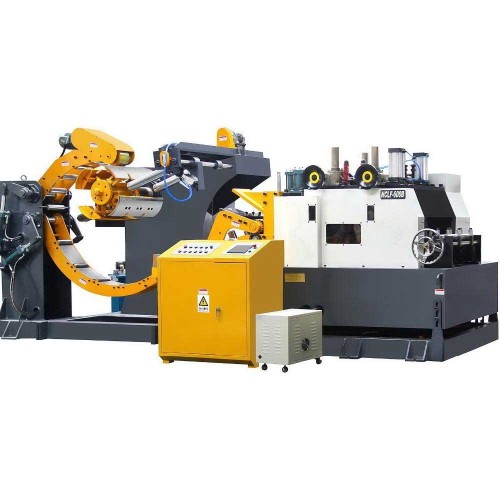
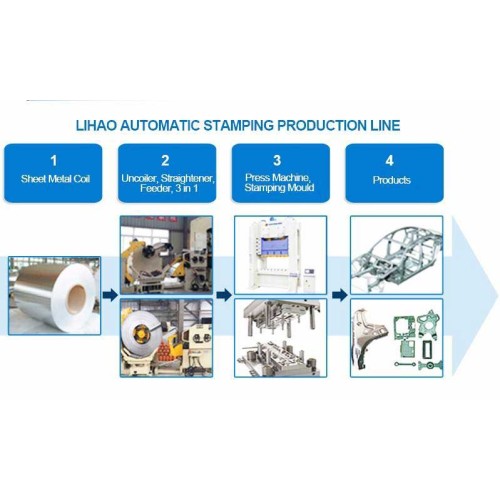






- Stock: In Stock
- Model: SCJ006868
- SKU: SCJ006868
Available Options
Ask a Question About This Product
- Specifications
Other attributes | |
Condition | New |
Place of Origin | Guangdong, China |
Weight (KG) | 6000 |
warranty: | More than 5 years |
Key Selling Points | Easy to Operate |
Use | Sheet |
Showroom Location | Malaysia |
Applicable Industries: | Manufacturing Plant |
Marketing Type | Hot Product 2019 |
Machinery Test Report | Provided |
uncoiler power | 1.5KW |
Video outgoing-inspection | Provided |
Warranty of core components | 1 Year |
Core Components | PLC, Engine, Bearing, Gearbox, Motor, Pressure vessel, Gear, Pump |
Material thickness | 0.2-2.0mm |
Material width | 50-400mm |
Power | Optional |
Feeding speed | 0-20m/min |
Max coil outer diameter | 1200mm |
Coil inner diameter | 508 |
Max coil weight | 3T |
Voltage | 380V |
Dimension(L*W*H) | Customized |
Feeding roller diameter | 66mm |
Straightening roller diameter | 48*11(up6/down5) |
Type | Straightener Feeder & Uncoiler |
Straightening power | 2.9KW |
Packaging and delivery | |
Packaging Details | plywood box, plywood pallet. |
Port | SHENZHEN |
Supply Ability | |
Supply Ability | 30 Set/Sets per Month |
- Description
Save Looping Space, Increase Safety Coiled material is from uncoiler through both left and right free guide rollers with advance photo sensors keeps looping. Through the opener device and bending roller system feeding the coiled material from up to down, passing opener device, coil tip flatness device, pinch rollers, work rollers, feed rollers to make the coiled material passing in an excellent smooth feeding
STANDARD ACCESSORY
1. Electric eye loop control system
2. Feed and straightener rolls hard chrome plated
3. Outgoing catenary to assist and support the material
4. Hold down arm device
5. Feeding line easily adjusted by advance worm gear screw jacks device
6. Uncoiler with inverter control
7. Reference indicator adjuster
8. Eccentric Roller (Upper)-easy to set up the up curve or down curve feeding exit direction
9. Hand-set coil width guide at outlet side
10. Hand-wheel-adjusted coil width guides at straightener inlet side
11. Threading table device
12. Coil tip de-bender
13. Uncoiler with air disc brake
14. A-frame type coil keeper
OPTION
1. Coil car
2. Shearing device
Model | Unit | NCHF-400B | NCHF-600B |
Material thickness | Mm | 0.3-2.2 (Straightening roller φ50x6up/6down) | |
Material width | Mm | 400 | 600 |
Coil inner diameter | Mm | Φ450-530 | |
Coil outer diameter | Mm | Φ1200 | |
Coil weight | Kg | 2000 | 3000 |
Decoiler power | Hp | 2 | 3 |
Straightening power | Kw | 1.8 | 2.9 |
Expansion style | - | Manual expansion | Hydraulic expansion |
Size | m | 3.8x1.7x2.3 | 3.8x2.4x2.3 |
Weight | T | ≈3.2T | ≈6T |
Electronic control configuration table:
Number | Name | Brand | ||
1 | servo motor | Yaskawa | ||
2 | 7 inch human-machine interface | Mitsubishi | ||
3 | 4.3 inch human-machine interface | Mitsubishi | ||
4 | Conventional motor | Taiwan TECO | ||
5 | Frequency converter |
| ||
6 | Pneumatic Components | SMC | ||
7 | PLC | Mitsubishi | ||
8 | Relay components, etc. | Schneider | ||
9 | power cable | Baosheng cable(Flame retardant) |
·Material part
The frame part of the material frame is welded by Q235B that has a certain elongation, good strength and toughness, and is easy to punch and weld. So it is widely used in the manufacture of general mechanical parts. The Q235B material is laser-cut to ensure the flatness of the whole plate. After straight cutting, the hole is machined by CNC to ensure the accuracy of the hole position.After the hole is processed, it is formed by CO2 protection welding to ensure that the size of the rack is fixed. Finally, the internal structure of the steel is changed by annealing heat treatment to improve the performance of the steel. The heat treatment process can not only strengthen the metal material to fully exploit the material performance potential, reduce the structural weight, but also improve the quality of the mechanical products and greatly extend the service life of the machine parts. At the same time, it can eliminate the defects caused by the welding process, eliminate the segregation, reduce the internal stress and make the structure and properties of steel more uniform.
·Material spindle
The spindle bearing bore is formed by a horizontal boring machine. The coaxiality is guaranteed to be below 0.015mm. The main shaft of the material frame is made of 40Mn tube forging. After spheroidizing annealing and quenching and tempering treatment, the flexibility of the main shaft is greatly enhanced, which is superior to the common carbon steel pipe commonly used in the industry. The shearing capacity maximizes the load carrying capacity of the spindle, so that the starting and stopping of the coil is smoother and the load of the motor is reduced.
·Left and right vertical board
The left and right vertical plates of the straightening head are made of cast steel ZG25 that has high strength, good plasticity and toughness, good welding performance, no deformation and high stability. The left and right vertical plates of each set of equipment will be opened with a mold, and then cast by ZG25, and then, by annealing, the material is exposed to high temperature for a long time, and then slowly cooled. The main purpose is to improve or eliminate various structural defects and residual stresses caused by steel during casting, forging, rolling and welding, to prevent deformation and cracking of the workpiece, to soften the workpiece for cutting, to refine grains and improve the structure to improve the mechanical properties of the workpiece, through the CNC pair processing, to ensure the accuracy of the right and left vertical plate holes and stability.
·Correct roller part
The correction roller is the core part of the Uncoiler ,Straightener,Feeder,3 in 1. The processing technology of Lihao Machinery is forged into round steel by GCr15. After pre-heat treatment (spheroidizing annealing),then it is stabilized by car, milling, intermediate frequency treatment and coarse grinding and deep cooling , then refining, and finally plating,which maximizes accuracy, concentricity, finish and hardness, extending the life of the correcting roller.
·Gear section
The gear machining process used by Lihao Machinery includes the following process: gear grinding processing - tooth surface processing - heat treatment- tooth surface finish grinding. The hair cultivating parts are mainly used for forging, and the normalizing treatment is carried out to improve the cutting.The gears are designed according to the drawings, followed by roughing, and then semi-finishing, car, rolling, and gear shaping, so that the gears are basically formed;then heat treatment is performed to improve the mechanical properties. According to the design requirements of the drawings, the final finishing, finishing the benchmark, finishing the tooth type. After the above treatment, our gear grade can reach 6 grades, high wear resistance, high strength and long service life.
- Reviews