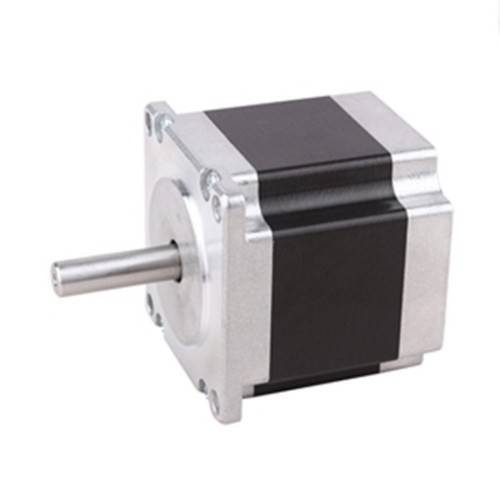
Nema 23 Stepper Motor, 2.8A, 1.8 degree, 2 phase 4 wires
from
$73.92
Ex Tax: $73.92
- Stock: In Stock
- Model: SCJ009413
- SKU: SCJ009413
Products Sold: 0
Product Views: 691
Available Options
Ask a Question About This Product
- Description
Nema 23 Stepper Motor, 2.8A, 1.8 degree, 2 phase 4 wires
Brief
2-phase 4-wire Nema 23 stepper motor, with 1.8 deg. step angle(200 steps/revolution). Each phase draws current 2.8A, allowing for a holding torque of 1.26Nm. and high quality, direct sale by manufacturer.
Description
Nema 23 Stepper motor, 1.26Nm in 56mm, 1.8 degree.
Specification
Electrical Specification | Model | SOCOJE57STH56-2804 |
Matched Driver Model | SCJ009413(Click it to see more info) | |
Step Angle | 1.8° | |
Holding Torque | 1.26Nm | |
Rated Current/phase | 2.8A | |
Phase Resistance | 0.9Ω | |
Inductance | 2.5mH | |
Rotor Inertia | 280g-cm2 | |
Physical Specification | Frame Size | 57 x 57mm |
Length | 56mm | |
Shaft Diameter | Φ6.35mm | |
Shaft Length | 19mm | |
Motor Leads | 4 | |
Weight | 0.68kg | |
Technical Parameters | Step Angle Accuracy | ±5% (full step, no load) |
Resistance Accuracy | ±10% | |
Inductance Accuracy | ±20% | |
Temperature Rise | 80℃ Max. (rated current, 2 phase on) | |
Ambient Temperature | -20℃~+50℃ | |
Insulation Resistance | 100MΩ Min. 500VDC | |
Dielectric Strength | 500V AC for one minute | |
Shaft Radial Play | 0.02Max. 450g | |
Shaft Axial Play | 0.08Max. 450g | |
Quality Assurance | Warranty Period | 12 months |
Certificate | CE, ROHs, ISO/SGS9001 |
Dimensions: (Unit=mm)
L Max=56mm
Wiring Diagram
Tips: How to solve the problem about heating of the stepper motor?
- Reducing heating of the motor means reducing copper and iron loss. There are two directions for reducing the copper loss, including reducing resistance and current. It is thus required to choose the motor with small resistance and rated current when selecting the motor. As for 2-phase motor, the parallel cannot be used if the series one could be used. However, it usually collides against the requirements of torque and high velocity.
- As for the selected motor, it is necessary to make full use of automatic semi-flow control and offline state functions of the stepper motor driver, as for former of which the current will be reduced when the motor is at static state while as for the latter of which the current is cut off.
- In addition, as the current waveform approaches the sine and has less harmonic wave, the heating of motor with subdivided driver is less. There are few methods or reducing the iron loss. It is related to the voltage grade. Though high voltage driver motor could lead to the rise in high speed characteristic, the increase in heating is also brought.
- It is necessary to choose drive motor with proper voltage grade, giving considerations into indexes such as stability, heating and noise, etc.
- Reviews