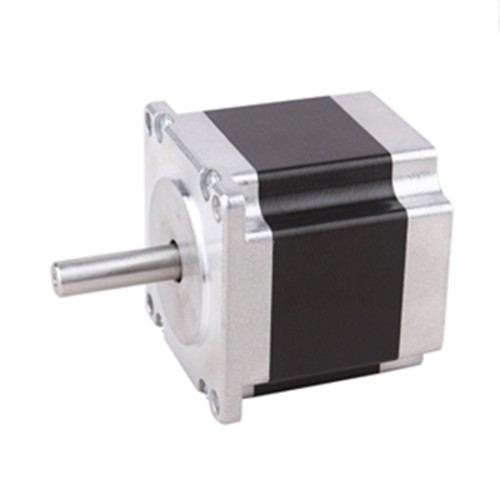
Nema 23 Stepper Motor Bipolar, 1.8 degree, 2A, 2 phase 4 wires
from
$69.15
Ex Tax: $69.15
- Stock: In Stock
- Model: SCJ009410
- SKU: SCJ009410
Products Sold: 0
Product Views: 625
Available Options
Ask a Question About This Product
- Description
Nema 23 Stepper Motor Bipolar, 1.8 degree, 2A, 2 phase 4 wires
Brief
Nema 23 Bipolar stepper motor with 1.8 deg. step angle. Each phase draws current 2A, allowing for a holding torque of 0.9Nm. and manufacturer direct sale.
Description
Nema 23 Stepper motor, 0.9Nm in 51mm, 1.8 degree, 2 phase 4 wires.
Specification
Electrical Specification | Model | SOCOJE57HS51-2004 |
Matched Driver Model | SCJ009410(Click it to see more info) | |
Step Angle | 1.8° | |
Holding Torque | 0.9Nm | |
Rated Current/phase | 2A | |
Phase Resistance | 1.2Ω | |
Inductance | 3mH | |
Rotor Inertia | 275g-cm2 | |
Physical Specification | Frame Size | 57 x 57mm |
Length | 51mm | |
Shaft Diameter | Φ8mm | |
Shaft Length | 19mm | |
Motor Leads | 4 | |
Weight | 0.65kg | |
Technical Parameters | Step Angle Accuracy | ±5% (full step, no load) |
Resistance Accuracy | ±10% | |
Inductance Accuracy | ±20% | |
Temperature Rise | 80℃ Max. (rated current, 2 phase on) | |
Ambient Temperature | -20℃~+50℃ | |
Insulation Resistance | 100MΩ Min. 500VDC | |
Dielectric Strength | 500V AC for one minute | |
Shaft Radial Play | 0.02Max. 450g | |
Shaft Axial Play | 0.08Max. 450g | |
Quality Assurance | Warranty Period | 12 months |
Certificate | CE, ROHs, ISO/SGS9001 |
Dimensions: (Unit=mm)
L Max=51mm, Shaft Length=L1-1.6mm, L1(Common)=20.6mm
Wiring Diagram
Tips: Methods for improving the stepping system precision
- Transmission interval compensation
Enhance the manufacturing and assembling precision of gear and screw of transmission elements of machine tool and take measures for eliminating the transmission clearance, but the transmission clearance cannot be completely eliminated.
When the motion or rotational direction of mechanical transmission chain is changed, numerous command pulses only could play the role of eliminating clearance at the very beginning. At as a result, the idle walk of the stepper motor is caused. However, the workbench cannot be moved actually. Thus, the transmission error is caused.
Compensation method: firstly measure and save clearance; when receiving reverse displacement command, firstly not output reverse pulse to the stepper motor but transfer the gap value into pulse number N to drive the stepper motor to rotate to span over the transmission clearance, and the act according to the command pulse. - Thread pitch error compensation
The manufacturing error in screw pitch of ball screw in transmission chain has direct influence on displacement precision of platen.
Compensation method: set numerous compensation points, measure and record displacement error of the platen at each compensation point to determine the compensation value and transmit it to the digital device as control parameter.
When the device runs, every time when the platen passes by each compensation point, the compensation quantity will added to CNC system to compensate screw pitch error. - Subdivision circuit
Subdivision drive: subdivide one stepping angle of stepper motor into numerous drive methods.
- Reviews