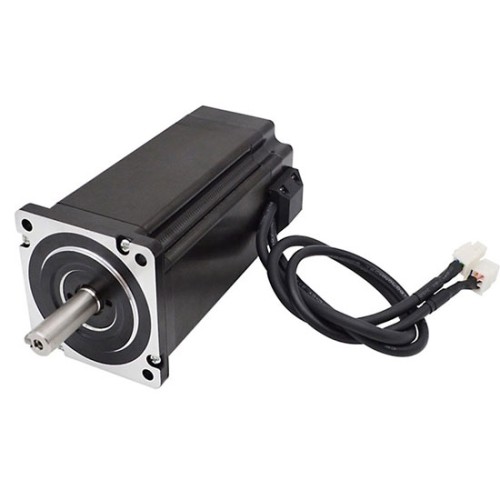
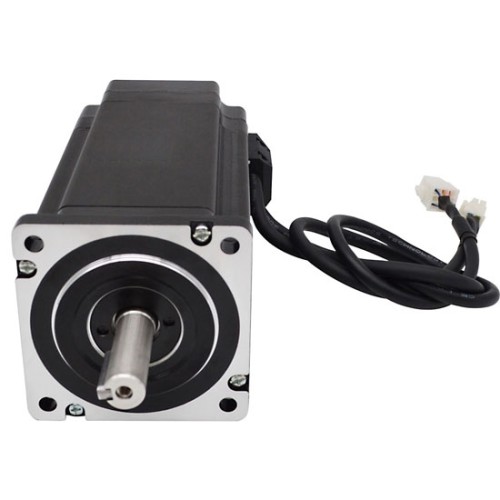

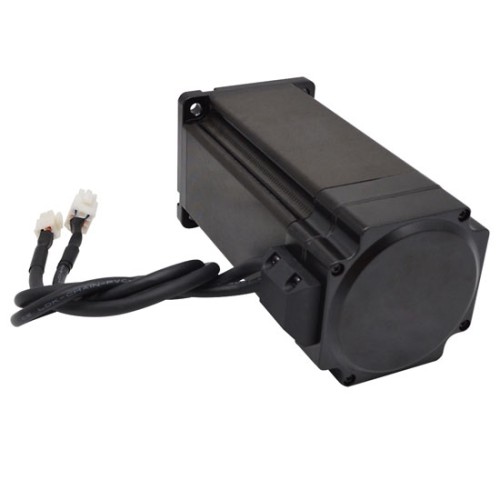






- Stock: In Stock
- Model: SCJ009354
- SKU: SCJ009354
Available Options
Ask a Question About This Product
- Description
Nema 34 Closed Loop Stepper Motor, 2 Phase, 6.2A, 8.2N·m
Brief
Description
SOCOJE Nema 34 closed loop stepper motor combines the advantages of servo motor and stepper motor technologies. It run more smoothly with less resistance than a standard stepper motor. This hybrid bipolar stepper motor with high holding torque of 8.2 N·m is suitable for the biggest projects, such as CNC application, robotic, 3D technology and so on.
Physical Specification
- Model Number: SOCOJE-FY86EL620BC1
- Matched the Driver Model: SOCOJE-FYDB808T
- Flanged Size: 86 x 86mm (Nema 34)
- Motor Length: 134mm
- Shaft Diameter: 14mm
- Number of Leads: 4 wire
- Weight: 3.6kg
Electrical Specification
- Motor Type: Bipolar Stepper
- Step Angle: 1.8°
- Rated Current: 6.2A
- Holding Torque: 820 N·cm (8.2 N·m, 1161 Oz.in)
- Phase Resistance: 0.45Ω
- Phase Inductance: 4.7mH
- Rotor Inertia: 3600g·cm2
Dimensions (Unit: mm)
L=134mm
Motor & Encoder Wiring Diagram
Speed-Torque Curve Diagram
Details
Tips: Difference between 2 phase stepper motor and 4 phase stepper motor
There are two phase stepper motors, four phase stepper motor and five phase stepper motors in the market. But no matter what kind of stepper motor, their working principle is the same. When current flows through the stator winding, the stator winding generates a vector magnetic field. The magnetic field will drive the rotor to rotate in an angle, so that the pair of magnetic field directions of the rotor are consistent with the magnetic field directions of the stator. When the vector magnetic field of the stator rotates by an angle. The rotor also rotates an angle with the magnetic field. Each time an electric pulse is input, the motor rotates one angle to move forward.
The angular displacement that it outputs is proportional to the number of input pulses, and the speed is proportional to the pulse frequency. Change the sequence of winding energization, and the motor will reverse. Therefore, the number of pulses, the frequency and the energization sequence of each phase winding of the motor can be used to control the rotation of the stepper motor.
The differences between 2 phase stepper motor and 4 phase stepper motor are:
- Different internal leads: there are 4 lead wires for 2 phase motors, and there can be 5 or 6 lead wires for 4 phase motors.
- Different ways of working: 2 phase permanent magnet motors have windings on the stator and the rotor is composed of soft magnetic materials. The structure is simple, the cost is low, and the step angle is small, up to 1.2 degrees. The 4 phase high torque motor is a permanent magnet stepping motor, its rotor is made of permanent magnet material, and the number of poles of the rotor is the same as that of the stator. Its characteristics are good dynamic performance and large output torque.
Documents
- Reviews