Your shopping cart is empty!
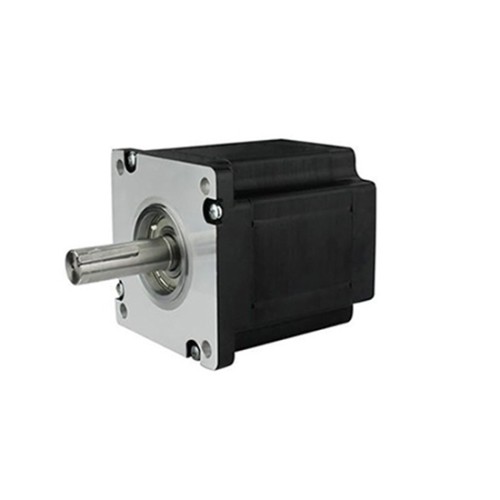
- Stock: In Stock
- Model: SCJ009348
- SKU: SCJ009348
Available Options
Ask a Question About This Product
- Description
3 phase Nema 42 Stepper motor 5A 1.2 degree 6 wires
Brief
Description
The Nema 42 stepper motor with 1.2 degree step angle, 3 phase 6 wires, high holding torque of 22Nm.
Specifications
Basics | Model | SOCOJE3150-5006A |
Matched the Driver Model | SCJ009348 (Click it to see more info) | |
Step Angle | 1.2° | |
Length | 150mm | |
Weight | 8.5kg | |
Current | 5A | |
Resistance | 1.2Ω | |
Holding Torque | 22Nm | |
Motor Leads | 6 | |
Rotor Inertia | 11000g-cm2 | |
Technical parameters | Step Angle Accuracy | ±5% (full step, no load) |
Resistance Accuracy | ±10% | |
Inductance Accuracy | ±20% | |
Temperature Rise | 80℃Max. (rated current, 2 phase on) | |
Ambient Temperature | -10℃~+50℃ | |
Insulation Resistance | 100MΩ Min. 500VDC | |
Dielectric Strength | 1Min. 500VAC·5mA | |
Shaft Radial Play | 0.06Max. 450g | |
Shaft Axial Play | 0.08Max. 450g |
Dimension
Wiring Diagram
Tips: Solutions to the power interference of stepper motor
At many occasions, due to the high current and voltage of the stepper motor, e.g.: For some stepper motor, the maximum current: 8A and voltage: 325V, and magnetic shielding of its shell is not implemented with aluminum alloy shell, the interference in high-sensitive receiver system is caused, so that it cannot work normally and power interference is also caused. Especially the frequency is high, normal communication cannot be realized on SCM and upper computer of the control system. If serious, SCM will be halted, then the difficulty will be brought to the normal use. Therefore, the interference should be solved.
Solutions to power interference of stepper motor are as below:
- Install power filter to reduce the contamination of AC power.
- Reduce the the external interference in power line with the shielded line or the interference of power line in external world.
- Based on the principle of "single-point-earthing", earth the grounding of power filter and stepper driver PE (the baseboard of driver and chassis should be insulated.), control pulse and direction pulse DIR-outgoing lines of short circuit, motor earthing line, cable protecting cover between driver and motor and shielded wire of driver to the earthing rod on wall of chassis, and good contact should be realized.
- Lengthen the distance between control line, power line (L and N) and motor drive line (U, V and W) to avoid crossing, e.g. when dealing with the driver installation site of two drivers of the same chassis in the double-shaft system, put the nameplate of one driver forward and that of the other backward, and shorten the leads as far as possible when making structural arrangement.
- Reviews