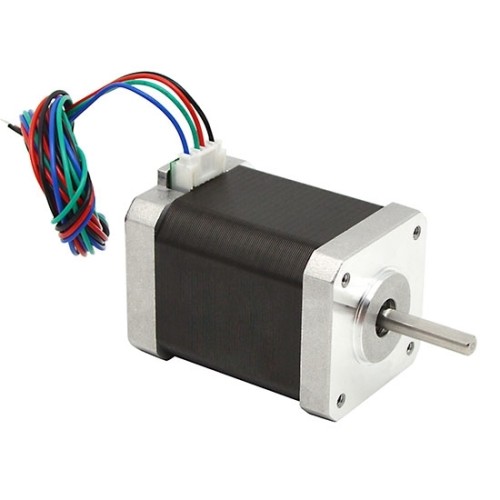
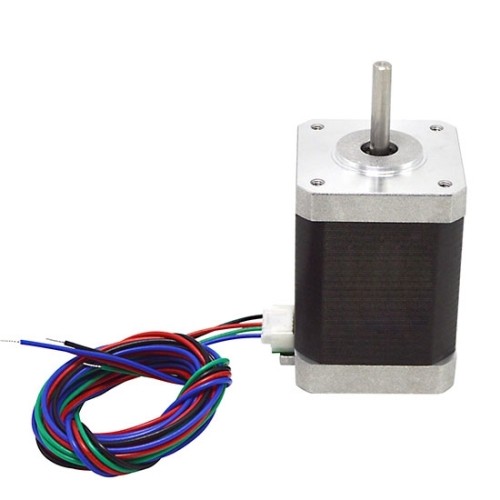
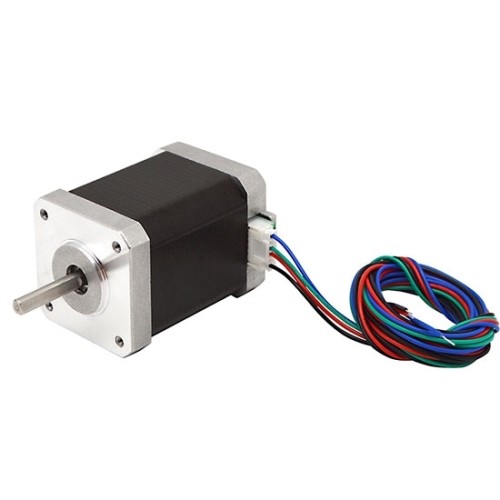
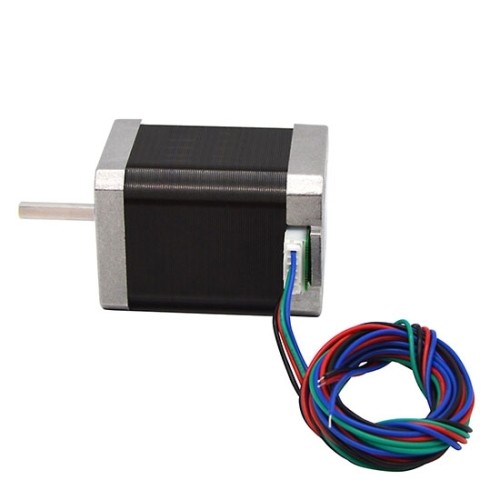
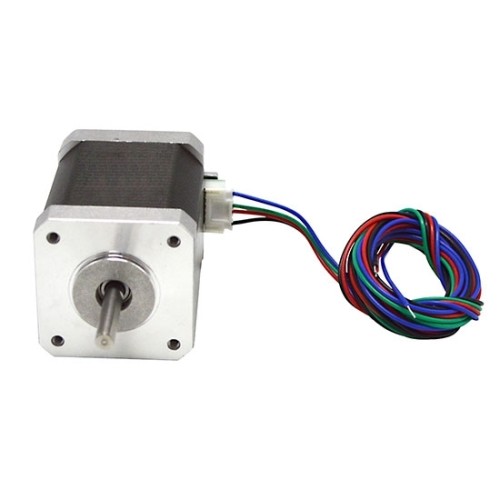





Nema 17 Stepper Motor, 2 Phase, 1.5A, 0.28N·m
from
$62.82
Ex Tax: $62.82
- Stock: In Stock
- Model: SCJ009417
- SKU: SCJ009417
Products Sold: 0
Product Views: 664
Available Options
Ask a Question About This Product
- Description
Nema 17 Stepper Motor, 2 Phase, 1.5A, 0.28N·m
Brief
small Nema 17 hybrid stepper motor for sale, 2 phase 4 wire lead, 1.5A, holding torque at 0.28N·m, step angle 1.8 degree, motor length 34mm, small size, high quality and high precision for CNC machine, 3D printer, sewing machine and electronic equipment.
Description
Bipolar two phase mini stepper motor with 5mm motor shaft, is used for robot arm, CNC router, 3D printer and other electronic machine. This permanent magnet stepper motor can driven by a DC 18 ~ 36V digital stepper driver for precise position control.
Physical Specification
- Model Number: SOCOJE-FY42ES150A
- Matched the Driver Model: SOCOJE-FYQM302A
- Flanged Size: 42 x 42mm (Nema 17)
- Motor Length: 34mm
- Shaft Diameter: 5mm
- Number of Leads: 4 wire
- Weight: 0.22 kg
Electrical Specification
- Motor Type: Bipolar Stepper
- Step Angle: 1.8°
- Rated Current: 1.5A
- Holding Torque: 0.28 N·m (28 N·cm, 40 Oz.in)
- Phase Resistance: 2.4Ω
- Phase Inductance: 4.5mH
- Rotor Inertia: 34g·cm2
Dimensions (Unit: mm)
L=34mm
Speed-Torque Curve Diagram
Details
Tips: Difference between stepper motor and AC servo motor
The stepper motor is a discrete movement device, which is essentially related to modern digital control technology. With the advent of all-digital AC servo systems, AC servo motors are increasingly used in digital control systems. Although the two are similar in control mode, there are differences in performance and applications.
- Different control accuracy
The step angle of the 2 phase hybrid stepper motor is generally 3.6°, 1.8°, and some high-performance stepping motors have a smaller step angle. The control accuracy of the AC servo motor is guaranteed by the rotary encoder at the back of the motor shaft. - Different low frequency
Stepper motors are prone to low-frequency vibration at low speeds. The vibration frequency is related to the load condition and the performance of the drive. It is generally considered that the vibration frequency is half of the no-load take-off frequency of the motor. The AC servo motor runs very smoothly, and there is no vibration even at low speeds. - Different moment frequency
The output torque of the stepper motor decreases with the increase of the speed, and the maximum working speed is generally between 300 and 600 rpm. The AC servo motor has a constant torque output, that is, it can output a rated torque within its rated speed, and a constant power output above the rated speed. - Different operating performance
The control of the stepper motor is an open loop control, and the AC servo drive system is a closed loop control. The driver can directly sample the feedback signal of the motor encoder. The position loop and the speed loop are formed internally. Generally, the stepping motor will not lose steps or overshoot. The phenomenon of rushing. - Different speed response performance
It takes 200 to 400 milliseconds for a stepper motor to accelerate from a standstill to a working speed. The AC servo system can accelerate from a standstill to its rated speed of 3000 rpm in just a few milliseconds, and can be used in control situations that require fast start and stop.
Documents
- Reviews