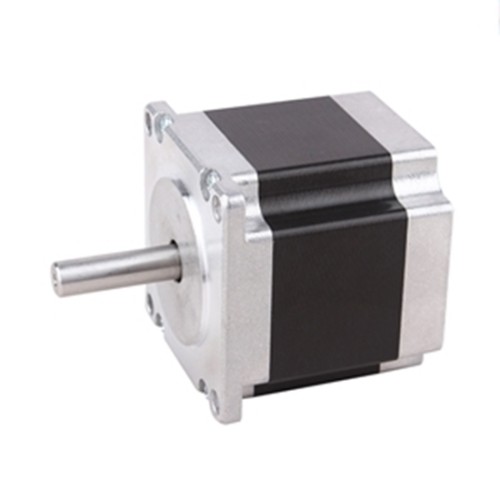
- Stock: In Stock
- Model: SCJ009402
- SKU: SCJ009402
Available Options
Ask a Question About This Product
- Description
Nema 23 2-phase Stepper Motor, 2.8A, 1.8 degree, 4 wires
Brief
Description
Nema 23 Stepper motor, 2.8A phase curent, 1.89Nm in 76mm, 1.8 degree.
Specification
Electrical Specification | Model | SOCOJE57STH76-2804 |
Matched Driver Model | SCJ009402(Click it to see more info) | |
Step Angle | 1.8° | |
Holding Torque | 1.89Nm | |
Rated Current/phase | 2.8A | |
Phase Resistance | 1.13Ω | |
Inductance | 3.6mH | |
Rotor Inertia | 440g-cm2 | |
Physical Specification | Frame Size | 57 x 57mm |
Length | 76mm | |
Shaft Diameter | Φ6.35mm | |
Shaft Length | 19mm | |
Motor Leads | 4 | |
Weight | 1.1kg | |
Technical Parameters | Step Angle Accuracy | ±5% (full step, no load) |
Resistance Accuracy | ±10% | |
Inductance Accuracy | ±20% | |
Temperature Rise | 80℃ Max. (rated current, 2 phase on) | |
Ambient Temperature | -20℃~+50℃ | |
Insulation Resistance | 100MΩ Min. 500VDC | |
Dielectric Strength | 500V AC for one minute | |
Shaft Radial Play | 0.02Max. 450g | |
Shaft Axial Play | 0.08Max. 450g | |
Quality Assurance | Warranty Period | 12 months |
Certificate | CE, ROHs, ISO/SGS9001 |
Nema 23 Stepper Motor Dimensions: (Unit=mm)
L Max=76mm
Nema 23 Stepper Motor Wiring Diagram
Tips: Application of stepper motor into mine hoisting
Stepper motor features simple structure, large power, convenience in maintenance, high positioning accuracy, good reliability, small volume and as many as 32 choices for the drive system,, no accumulated location error, self-locking and low cost, so it is widely applied. Additionally, along with the application control of SCM using mature microcomputer technique, automatic control can be easily realized. Above characteristics completely meet the requirements of micro drive. Besides, automatic control of mine hoisting system and unattended duty hoisting system can be realized.
As for the control process of the stepper motor during mine hoisting, firstly, mine hoist reducer approaches the crawling stage and the velocity is reduced to about 3m/s, the electromagnetic valve is powered on with automatic control system. The electromagnetic valve rod overcomes the elastic force shift down of spring under the role of electromagnetic force so that the compressed air enters the cavity B from A and enters the gasbag clutch through hollow shaft of reducer, so that micro drive device can be connected with the host.
When the velocity is continuously reduced the crawling speed, the dynamic brake power of the main motor is cut off by controlling the circuit. The hoister crawls at stable low velocity from stepper motor drive. By hoisting the vessel to the end point to unload, control circuit to cut off the electromagnetic valve, so that the stepper motor is separated from main engine to complete the crawling process for once. Then, follow the next cycle, by improving and reducing the occurrence rate of accidents when unloading, the safety of coalmine production can be enhanced and foundation for automation production of the coalmine can be laid.
- Reviews