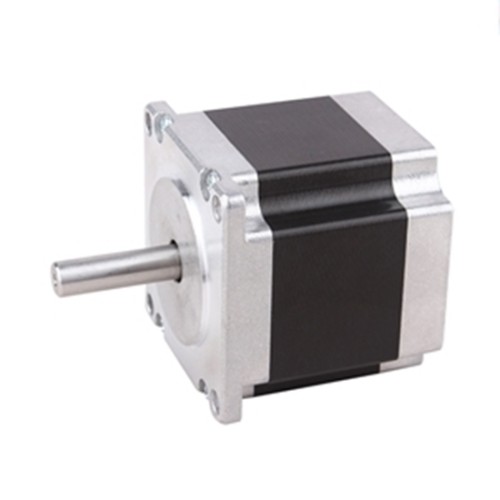
Nema 23 Stepper Motor Bipolar, 1.8 degree, 1.5A, 2 phase 4 wires
from
$69.15
Ex Tax: $69.15
- Stock: In Stock
- Model: SCJ009409
- SKU: SCJ009409
Products Sold: 0
Product Views: 641
Available Options
Ask a Question About This Product
- Description
Nema 23 Stepper Motor Bipolar, 1.8 degree, 1.5A, 2 phase 4 wires
Brief
Bipolar stepper motor Nema 23, 1.5A and 1.6 ohms, 2 phase 4 wires, 0.82 Nm holding torque, 1.8 deg. step angle, brand new and manufacturer direct sale.
Description
Nema 23 Stepper motor, phase current 1.5A, 0.82Nm in 51mm, 1.8 degree.
Specification
Electrical Specification | Model | SOCOJE57HS51-1504 |
Matched Driver Model | SCJ009409(Click it to see more info) | |
Step Angle | 1.8° | |
Holding Torque | 0.82Nm | |
Rated Current/phase | 1.5A | |
Phase Resistance | 1.6Ω | |
Inductance | 3.8mH | |
Rotor Inertia | 275g-cm2 | |
Physical Specification | Frame Size | 57 x 57mm |
Length | 51mm | |
Shaft Diameter | Φ8mm | |
Shaft Length | 19mm | |
Motor Leads | 4 | |
Weight | 0.65kg | |
Technical Parameters | Step Angle Accuracy | ±5% (full step, no load) |
Resistance Accuracy | ±10% | |
Inductance Accuracy | ±20% | |
Temperature Rise | 80℃ Max. (rated current, 2 phase on) | |
Ambient Temperature | -20℃~+50℃ | |
Insulation Resistance | 100MΩ Min. 500VDC | |
Dielectric Strength | 500V AC for one minute | |
Shaft Radial Play | 0.02Max. 450g | |
Shaft Axial Play | 0.08Max. 450g | |
Quality Assurance | Warranty Period | 12 months |
Certificate | CE, ROHs, ISO/SGS9001 |
Dimensions: (Unit=mm)
L Max=51mm, Shaft Length=L1-1.6mm, L1(Common)=20.6mm
Wiring Diagram
Tips: Inspecting methods for inhibiting noise of stepper motor
When the stepper motor is driven, if there is obvious noise and vibration is caused to the stepper motor, it is necessary to inspect according to the following steps:
- Whether the stepper motor is matched with the driver, that is key. If not matched, it may be useless to take following steps such as subdivision, drive current and speed adjustment. It is therefore advised to buy the complete set and ensure it is the original when choosing the stepper motor and driver.
- At the present, the stepper motor driver is divided into digital and analog types. The noise of the analog stepper motor driver is large when it is started but it is basically no for the digital one, for which the reason is generally for one DSP chip is added to the digital driver to optimize the stepper motor drive. Therefore, to ensure the noise and vibration is as small as it is, it is advised to use the digital stepper motor driver.
- Correctly adjust the subdivision and current of the stepper motor driver, the larger the subdivision the smaller the change amplitude of coil in motor. That is, the noise is mitigated. As for subdivision, it is advised to set it as 8 and above. Under the circumstance that there is enough torque to drive the load for the stepper motor, it is also necessary to reduce the driver current. The smaller the parameter set the small the change amplitude of the coil in the motor.
- Correctly set the acceleration and deceleration and highest rotational velocity of the stepper motor. The experiment shows that it is easier to generate additional noise during the acceleration of the stepper motor. The solution is to increase the acceleration and deceleration of the stepper motor appropriately under the circumstance that acceleration and deceleration doesn’t cause step out.
- Reviews