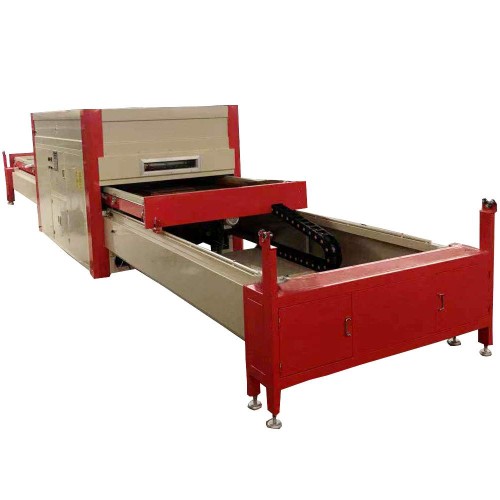
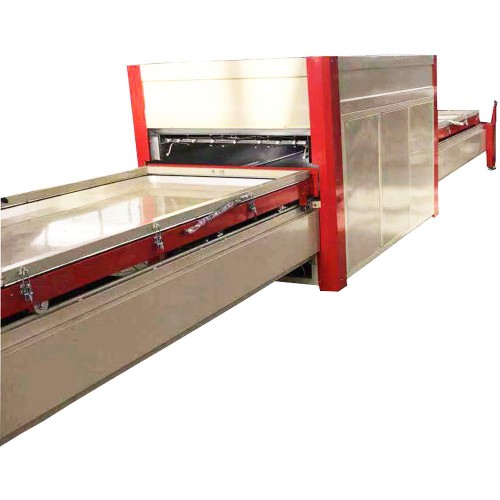
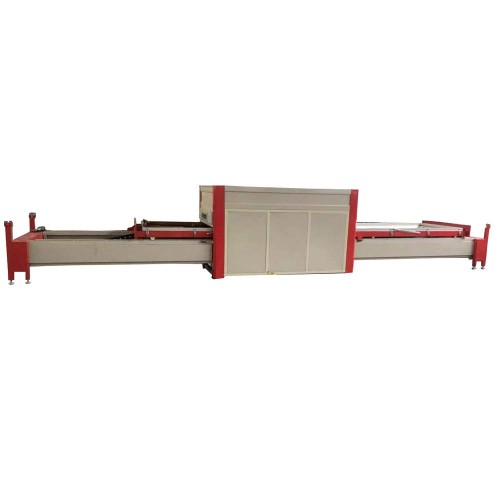
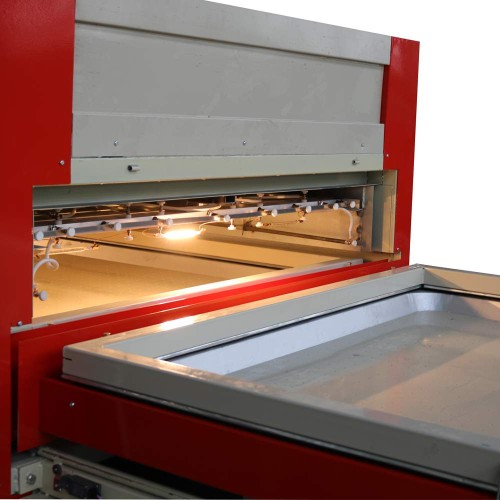




Wood Door Membrane Press Machine 220V 60Hz
from
$4,200.27
Ex Tax: $4,200.27
- Stock: In Stock
- Model: SCJ006552
- SKU: SCJ006552
Products Sold: 0
Product Views: 284
Ask a Question About This Product
- Description
Wood Door Membrane Press Machine 220V 60Hz
About this product
1. 3D foil and veneer lamination
2. One or two trays
3. Membrane or membrane-less pressing
4. 220V,3-phase
5. 26.8 HP Motor
Product Description
Product Description
Membrane presses are used for kitchen cabinet doors, closet doors, store fixture parts, and office furniture tops.
· 75% power cost saving
· 80% more production
· Highly flexible press cold/hot/vacuum/single membrane/double membrane
· Heavy duty machine
· Very high value for money
The new membrane press is designed for a variety of 3D products using veneer and/or rigid thermo foil.
Ideal for a new product or manufacturing start-up of 3D components, this press line has the ultimate combination of flexibility and productivity.
Available with one or two trays, the Eagle will produce high quality components from materials such as PVC, PET, Kydek, standard rigid thermo-plastic foils and veneer.
Membrane Preservation Tips
- Cleaning. Lamination projects require the use of a clean membrane. If you find yourself needing to remove any dirt from your membrane, remember to use a solution that consists only of water and mild dish soap. Steer clear of solvents, mineral spirits, alcohol, and acetone. These solutions can weaken the membrane, potentially causing premature failure.
- Raiser Board Sizing. Before you begin your membrane pressing process, ensure your raiser boards are the correct size. Raiser boards that are too small can cause membrane ruptures because they pose the problem of providing too much space underneath the door being pressed, creating stress. Additionally, this issue can cause the door to break, which can then result in a damaged membrane. Raiser boards should be no more than ½" smaller than the part’s thickness along any one side.
- Positioning. Similarly, your membranes run the risk of damage if the parts being pressed are not positioned properly. Positioning your parts too close to one another or too close to the edge of the press tray can result in membrane tears. This is because the membrane will have to overstretch to fill in gaps that are too narrow. When pressing ¾" thick parts, position each no less than 2" away from one another and 2 ½ – 3" from the edge of the pressing tray. For parts with thicknesses greater than ¾", increase spacing accordingly.
- Foil Laminate Temperature. When pressing foil laminates, it is extremely important to ensure the laminate is up to the right temperature. If it is too cold, it will be too stiff to form properly and could easily shatter. Torn laminate edges will cut through membranes like a knife. Remember that sudden drops in ambient temperature, such as the onset of winter, need to be compensated for in order to keep the foil laminate and board temperatures ideal for membrane pressing.
- Tearing. If you’ve noticed that your membranes continuously tear in the same general location during the pressing process, you may be dealing with a rough spot on the contact metal. Examine the portion of your press that is contacting the membrane to check for rough patches of metal that may be causing wear and tear.
- Leaking. A perfect seal around the membrane pressing tray is crucial. Therefore, if the vacuum system in the press has leaks, or is otherwise not working properly, your membrane will be subject to more resistance, particularly with complicated contours. Check for vacuum leaks to avoid premature wear.
- Idle Time. Sometimes projects require idle time between presses. If this is the case for your project, be sure to keep the membrane away from the heating plate. Prolonged exposure to the heat source will weaken the membrane.
- Trimming. If you need a smaller membrane for your press and you opt to trim a standard size, you must be very precise. Keep the membrane truly rectangular in shape. This is important because if the membrane is no longer rectangular, it cannot be tensioned properly, causing overstretching. Overstretching will cause membrane ruptures. Also, uneven tension can create unwanted wrinkles throughout your laminate.
Product Information
Technical Details
Power | 220V,3-phase |
Motor | 26.8 HP |
Machine Size | 37"×69"×67" |
Working Size | 100"×51"×2" |
Additional Information
- Reviews